Week 2 of Stepcraft 840!

There's been some ups and downs with my first attempts but I'm really quite pleased! Really have learnt a lot, particulary trying over ambitious attempts before the machine was properly set up and the importance of checking, checking and checking again before sending files to cut.
Here's the first few thing I've cut.
There should of been 30 of these but a self inflicted Y error put a stop to that (still all the scrap MDF came in useful later).
Remember 1/4" is NOT 6mm - very sloppy pockets!
This was an experiment, although it failed (0.8mm ply fell apart after cutting) I was really quite pleased. It's a 1/50 scale wheel house of a model ferry.
Here is a Dibond sign I have made for an exhibition my company is attending. Cut unbelievably well with a 2mm up-cut, full speed and 3.4m per minute feed.
Where all that wasted MDF came, in making up stands for the letters.
SC840, HF500, UCNNC, Vcarve Pro, Turbo Cad

Very nice, keep posting your upcoming projects! 😉
Stepcraft 2 840
Kress 800 FME
UCCNC + UC100
V-Carve + QCad

Update on exhibition project using my Steppi - Remember don't use your Stepcraft at 1:30am when tired, you Will make (expensive) mistakes!
This the completed exhibition stand, the main stand is constructed of MDF cutting with a track saw and hand router.
This is name plate machined from 12mm moisture resistant MDF with a Dibond logo pocketed in, first mistake the pocket was tight and I damaged the dibond trying to fit it!
This went well again 12mm MDF and Dibond logo - I made the pocket slightly over sized this time.
The finished and mounted name and logo.
Two thing went wrong here, firstly the extreme end of the Y axis flexed enough for the V cutter not to properly on the logo and the start of the name. I think that either I will try and fit some internal support under the bed or fit a 18mm spoil board. I'm gaining to look at at making a vacuum table shortly, probably 2 sheets of 9mm MDF so that might solve the problem.
The second thing to go wrong (because of working tired) I copied a larger tool in Vcarve to create a 3mm end mill but left the 9mm first path in the setting. To the HF500's credit it plowed through the Dibond on the Y cut turned round onto the X, went a bit, stalled losing it's Y steps and carried on plowing through middle of the workpiece :sick: No spare material!
Again I'm really pleased with the Stepcraft, it really is impressive on fairly heavy work.
SC840, HF500, UCNNC, Vcarve Pro, Turbo Cad

The second thing to go wrong (because of working tired) I copied a larger tool in Vcarve to create a 3mm end mill but left the 9mm first path in the setting. To the HF500's credit it plowed through the Dibond on the Y cut turned round onto the X, went a bit, stalled losing it's Y steps and carried on plowing through middle of the workpiece :sick: No spare material!
.
CNC does not forgive a single mistake 🙂 Super stuff! looks great.
Hi, great work, do you have the dxf of the Heart?
Thanks
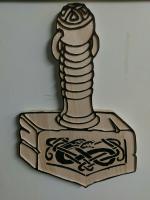
Hy.
very great works you have made!!
:woohoo: :woohoo:
Wenn du heute nur das tust - was du gestern schon getan hast - dann bleibst du auch morgen nur da - wo du heute schon bist
Rüdiger
☺☺☺ Lass mal späne produzieren!!! ☺☺☺
Pro Vario 10-05 D200 / Estlcam / WinPcNc USB / Kress 800
vorher: 600er / Estlcam / Mach3 UC100 mit USB Anschluss,HF500
Nice!
I need to get back into it, I made couple little things and now sidetracked with 3d printing.
In case anyone wondering what to do about the plywood getting ripped up, use a single straight flute bit.
curved bits pulls up or down makes a mess of plywood.
Stepcraft 600 v2 w/UC100 and UCCNC, Dremel, Cut2d, QCAD
- 44 Foren
- 7,441 Themen
- 63.5 K Beiträge
- 8 Online
- 26.5 K Mitglieder