Grounding of the system
I had to do a rush job to recreate some parts that were lost. I used a tooling block material (blue - high density). The milling programs were very large. The job failed more than 3 times, and in the end I had to hand fabricate the parts to meet the deadline.
I think the main cause of failure is due to insufficient grounding within the stepcraft system. I was trying to hoover up dust created by the milling and on one occasion I got a small static shock and at exactly the same moment the machine stopped but the program kept on running on the computer.
I guess this is a cautionary tale for when users might be machining materials that could be susceptible to building static, as well as hopefully providing a place to discuss way's in which the system could be grounded better to try to reduce instances of static electricity disrupting the machine and the USB controller.
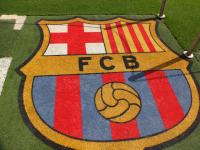
Hi coanda,
you speak about "better" grounding. Did you install the grounding cable delivered with the machine? If this is not installed there is NO grounding I would say.
Since I'm using a China spindle with a metal body my system is grounded from the end-mill via spindle grounding cable to the controller and the Stepcraft machine. So no problems until today but maybe your material is extremly prone.
Viele Grüße
Hartmut
V2/420 China 800W wassergekühlt
UCCNC & ARDUINO ESTLCAM Controller
ESTLCAM & QCAD
-----------------------------------
DK5LH/G11

Neither version is sufficient. The Aluminium is eloxated and does not conduct. And due to the coating, a grounded spindle might not ground the z axis as well. The airflow of a vacuum cleaner alone can lead to statical charges.
I added wires to connect all the axles.
In the German section of the forum there even was an collective order to buy antistatic vacuum tube. The problem is not only, that the high voltage is discharged via the SC electronics, it's also about the discharge sparks, which produce electromagnetic waves that can corrupt signals on not shielded wires.
So, you also might want to check selfmade Arduino wiring in case of mysterious problems.
I have a fixed parallel board and connect it to my USB boards with a quality shielded parallel printer cable.
SC 420 mit DIY parallel + Proxxon mit Mod + HF500 + SprintLayout + LibreCAD/QCAD + FreeCAD +WinPC starter/USB->EstlCAM + EstlCAM LPTAdapter + EstlCAM Handrad + DIY Vakuumtisch
Gruß, Andreas
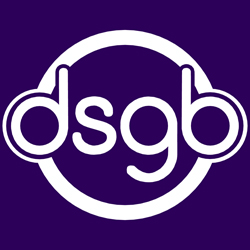
coanda,
I had no problems like this until recently when I connected my vacuum exhaust hose directly to a DIY dust shoe whereas previously I used the Stepcraft exhaust adapter and hose as an intermediate stage.
I believe that the problem was caused by the vacuum cleaner hose having exposed metal inside (plastic coated outside) and that the action of the wood particles blasting past generated static electricity. Previously this was well isolated from the machine because I used the Stepcraft hose which is softer plastic and, I presume, anti static.
When cutting an ebony guitar fretboard blank, I saw a static discharge after a few minutes and this stopped the machine and caused lost steps.
I have since sourced an anti static vacuum hose but it is not quite the correct size and is very inflexible so I will need to keep looking. In summary, if you do an internet search for static build up in machine exhaust extraction systems, you will find that this is a common problem. If you have installed the machine grounding cable to electrical socket, and are using an anti static suction hose, you should not experience any problems.
Doug
Stepcraft 2/840, StoneyCNC industrial HF spindle, 4th axis, TurboCAD 2016 Professional 64 bit, MeshCAM, GWizard feeds & speeds calculator, UCCNC
Hobby use: guitar building (luthiery), https://dsgb.net
This was the last time I used my Stepcraft printer - life got in the way. However, I now have need of it again - routing carbon fibre flat plate parts. I note that there was talk of a grounding lead - I did not receive a grounding lead with my stepcraft kit. Can someone point me in the direction of what/how/where this should be?
I will keep in mind about not using the vacuum nozzle directly, and use the shoe. However, this was not the only cause. There must have been static build up in the dust as I did not always use the vacuum directly and the machine still stopped working. Soon I will need to use a similar tooling board/modelling board again to make moulds so I need to bottom this out.
Many Thanks,
coanda
I guess, any point on the metal case inside the cnc would be a ok point to connect the ground? i wonder since it kinda like small round holes in my guides i X and Y, but if they are NOT conductive that can not be it..
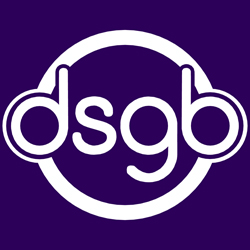
I had issues with static build up because the first tubing/hose I used was not anti-static. You can find anti-static tubing/hose no problem. An earthing/grouding lead is a good idea too I looked into this but it is better to earth/ground the body to a point away from the machine. The machine itself sits on rubber feet so is inherently insulated from the ground.
Regards.
Doug
Stepcraft 2/840, StoneyCNC industrial HF spindle, 4th axis, TurboCAD 2016 Professional 64 bit, MeshCAM, GWizard feeds & speeds calculator, UCCNC
Hobby use: guitar building (luthiery), https://dsgb.net
Thanks for the replies. As I get my workshop sorted out, I'll clean my machine from top to bottom and look to do what has been suggested here.
- 44 Foren
- 7,440 Themen
- 63.5 K Beiträge
- 4 Online
- 26.5 K Mitglieder