Stepcraft Keeps Milling Slightly Deeper

All,
I have had my Stepcraft 840 for about a week and am learning a lot. So, this may have an obvious answer to a newbie.
I am trying to mill 4 grooves 1/2" wide, 1/2" deep and 6" long. I am using a 1/8" end mill cutting 1/8" in each pass. I am using a spindle speed of 12000 and a feed rate of about 1200. Plunge rate is 20.
My problem is that each groove is about 1/16" deeper than the previous one. So, the first groove is 1/2" deep as it should be, and the last one is about 11/16" deep. Since the order is in a circle, it is not the level of my tabvel or board. The deepest groove ends up right next to the correct one.
I checked the G-Code. It has the correct depth on all groves.
It seems to be losing steps on the z-up movement. However, after the cuts are made, GoTo Zero goes to the correct location.
Any thoughts???
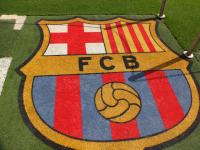
Hi Mark(?),
since nobody has answered so far I hope I can help a little bit but a native English speaker and someone who´s an expert in imperial values will do better. :woohoo:
Your workpiece is wood? You did not tell us... 🙁
I would cut only 85-90% of 1/8'' in each pass, not 100%. But this will not solve your problem.
- rpm 12000 is ok for wood
- feedrate: I would use 1000mm/min (millimeter... please convert yourself 😉 )
- plunge rate 20mm/min would be ok
- What deep per pass? I would use 1-2mm/pass.
Hope that helps a bit.
Viele Grüße
Hartmut
V2/420 China 800W wassergekühlt
UCCNC & ARDUINO ESTLCAM Controller
ESTLCAM & QCAD
-----------------------------------
DK5LH/G11
Hi,
To find out what goes wrong:
- Re-attach your plate (upside down) to the machine.
- Do this in the exact same place and in exactly the same way.
- Take a picture.
- Zero the z-axis 0.1" above the plate.
- Cut a square of approximately 8" by 8" and 0.01"deep.
- Repeat this each time 0.01 "deeper until the milling bit goes into the plate.
- Create another photo.
- Attach both photos to your answer.
Kilroy
Hi Mark,
One comment you made has worried me -
"However, after the cuts are made, GoTo Zero goes to the correct location."
If that is really true, then the Z-axis cannot be losing steps surely? Can you confirm that the end of the tool ends up in exactly (X and Y and Z) the same position as when you started the machining cycle??.
If that is the case, then surely some incremental offset is being added at each successive groove (pocket). It would be worth repeating the exercise and checking the DRO values and tool offsets between each pocket.
Peter
SC 420/2, Industrial VFD spindle from StoneyCNC
UC100 + UCCNC
Cut2D, Autosketch10, Draftsight, Eagle 9.5.1
There is no problem, however simple, that cannot be made more complicated by thinking about it.
Has your problem been resolved?
If so, how did you solve it?
If not, good luck
Kilroy
- 44 Foren
- 7,436 Themen
- 63.4 K Beiträge
- 1 Online
- 26.5 K Mitglieder