Dear user, the forum software has been updated. For the first login please reset your password.
Back to zero?

I'm sorry if this has been addressed before but if it was I couldn't find it.
I needed to make a hole grid on a 9mm plywood to serve as a baseplate for my S600, in order to hold a clamping system like this guy did.
This consisted of a 8x12 grid of 6mm and 12mm diameter holes, half of each. Also I needed to cut 9mm holes to a depth of 5mm concentric to the 6mm holes to house the clamp nuts. I used a 3mm flat end tool to mill everything out, feed 240mm/min, layers 1.5mm deep.
It all went well and nicely, with what I think were slow feed and gentle plunge in order to avoid problems.
First task was the 6mm holes, then another pass for the concentric 9mm holes, and finally the 12mm. Trouble was that the first batch was ok, but the concentric holes where not really so, and the 12mm ones were out of alignment.
At the end I sent the spindle back to the job 0,0,0 but the Y-axis was out by circa +5mm. X and Z axes were ok. Y-axis is well lubed and runs well from o to 590 with no funny noises. Both pillars are aligned.
Any comments please?
Clockwork Orange is a S600 with 4th axis, Kress 1050. Software is UCCNC, DeskProto, Rhino, DraftSight. Also a Silhouette Cameo for vinyl, plastic card, etc.
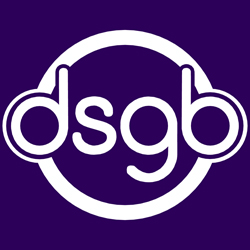
I can only think of obvious and generally unhelpful comments like:
"the machine has lost steps".
If the axes are indeed working well unloaded, an axis has met resistance so it's down to whether your toolpath and feeds/speeds parameters are sensible or not.
I.e. are you trying to cut too much material away in one of the passes?
Doug
Stepcraft 2/840, StoneyCNC industrial HF spindle, 4th axis, TurboCAD 2016 Professional 64 bit, MeshCAM, GWizard feeds & speeds calculator, UCCNC
Hobby use: guitar building (luthiery), https://dsgb.net

Losing steps as in loose clutch slipping back? That's a problem as I had already made all tasks slow in order to avoid loads. Tomorrow I'll try running a test track from a o point slightly off from Home to the end limits and back to 0 to see how it recentres in no-load.
This was one of the tests that some 20 years ago I used to run on A0 pen plotters before we bought them 🙁
Clockwork Orange is a S600 with 4th axis, Kress 1050. Software is UCCNC, DeskProto, Rhino, DraftSight. Also a Silhouette Cameo for vinyl, plastic card, etc.
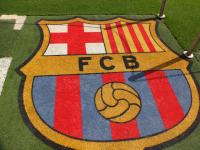
I would say the Y-axis belt is not adjusted properly. I tighten mine very strong.
Try also milling with the end-mill some mm above surface and see what will happen.
Viele Grüße
Hartmut
V2/420 China 800W wassergekühlt
UCCNC & ARDUINO ESTLCAM Controller
ESTLCAM & QCAD
-----------------------------------
DK5LH/G11
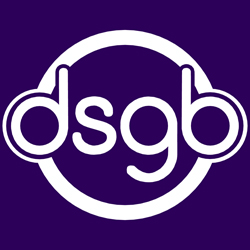
I would say the Y-axis belt is not adjusted properly. I tighten mine very strong.
Try also milling with the end-mill some mm above surface and see what will happen.
Agreed. The Stepcraft U.S. assembly video put me in fear of having too tight a belt which was a mistake. Another area where Stepcraft leaves the user to guess what a suitable tension is.
I then experienced big issues a couple of weeks ago until I put a decent amount of tension on the belt. Problem solved.
I have commented before but I was horrified to see on another of the Stepcraft U.S. setup videos which showed their XZ module stuck fast in the track extrusion so that it would only move when jerked fairly strongly! My gut feeling was that was nonsense so I tuned mine so that the assembly would run freely under gravity when the extrusion was tilted.
Doug
Stepcraft 2/840, StoneyCNC industrial HF spindle, 4th axis, TurboCAD 2016 Professional 64 bit, MeshCAM, GWizard feeds & speeds calculator, UCCNC
Hobby use: guitar building (luthiery), https://dsgb.net
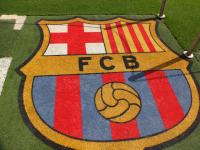
I would say the experience with mechanics is different for each user. That means for example "tighten a screw firmly" is very different if there is no reference or experience.
I've done modelmaking on ships, planes, helicopters, cars and railway-models for more than 35 years and that gave me a "feeling" what is correct and what not.
Maybe one step in the correct direction could be listing a torque value for each relevant screw. Don't know if that helps...
A second one could be a list of FAQ's and answers:
- I'm loosing steps, what to do..
- Circles are not round, what to do...
- my X-axis stuck...
- ...
Viele Grüße
Hartmut
V2/420 China 800W wassergekühlt
UCCNC & ARDUINO ESTLCAM Controller
ESTLCAM & QCAD
-----------------------------------
DK5LH/G11
Hartmut,
I think your idea is an excellent one - perhaps we need an independant "Wiki-step", whereby questions can be posted and relevant answers recorded. I know there is a CNC-wiki, unfortunately only in German, which could act as a model for "Wiki-step". Additional information such as videos and build pictures etc. etc. could be added a well. Your torque settings could be incorporated too.
Unfortunately someone would have to "police" such a site to ensure that only qualified answers were accepted, and to remove irrelevant or incorrect material and chit-chat. Then of course there would be a funding issue - I personally have no idea of the costs involved in maintaining such a website.
Any bright ideas on how to start such project?
Peter
SC 420/2, Industrial VFD spindle from StoneyCNC
UC100 + UCCNC
Cut2D, Autosketch10, Draftsight, Eagle 9.5.1
There is no problem, however simple, that cannot be made more complicated by thinking about it.
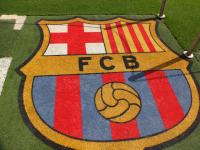
Hi Peter,
my ideas are more adressed to Stepcraft themself. 🙂 I'm not interested to do their quality assurance ...
So I like to help here from time to time but not with permanent commitment.
The idea with the torque settings can be simply implemented with no further effort from Stepcraft if done once. The wiki idea indeed needs permanent support and for sure during the start-phase it will be a lot of work.
The guy who`s hosting the German wiki (Speedo) could do that also in English if he likes...but he always ask for support... :whistle:
Viele Grüße
Hartmut
V2/420 China 800W wassergekühlt
UCCNC & ARDUINO ESTLCAM Controller
ESTLCAM & QCAD
-----------------------------------
DK5LH/G11

Thank you for your input Gentlemen :cheer: As a matter of fact the belt is taut enough though I cannot say how taut in BTUs/second 😆 but I know I'm not having it jumping teeth between both branches of the Y-axis.
I did a couple of test runs of my previous long toolpaths on no-load, and still I get differences between Zero at start and at end on Y-axis, the others being spot-on. To me it looks like I have to tune the entire Y running gear again, rollers and screw nut. This screw nut is very very sensitive as it is too easy to misalign and distort the Y-screws.
Clockwork Orange is a S600 with 4th axis, Kress 1050. Software is UCCNC, DeskProto, Rhino, DraftSight. Also a Silhouette Cameo for vinyl, plastic card, etc.
Hi Miguel
How annoying that the Y-axis needs tuning again - its a real pain.
When I tuned mine, I made sure that the moving rollers were all slackened off when I adjusted the end plates. That way I could be sure they were not the cause of any tightness. It's important to make sure the two gantry sides are equidistant from the end plates too (i.e. the X-axis is at 90 degrees to the Y-axis).
Having completed that adjustment, the rollers were then tightened individually so that they could just not be turned by hand (finger). I carefully degreased everything before doing this so I could feel the increase in resistance to turning as they were screwed down. Of course it was all lubricated again once I was happy with the adjustment.
I know Stepcraft suggest a 1/4 turn - IMHO that is a nonsense, it leads to grossly excessive forces and is likely to cause surface damage to the aluminium extrusions and the rollers themselves.
As a kinematic design that part of the system is very poor - in fact the rollers should cylindrical and not dished to match the extrusion. At least that would remove 4 unnecessary contacts and eliminate any twisting effect on the gantry sides.
Regards,
Peter
SC 420/2, Industrial VFD spindle from StoneyCNC
UC100 + UCCNC
Cut2D, Autosketch10, Draftsight, Eagle 9.5.1
There is no problem, however simple, that cannot be made more complicated by thinking about it.

Thanks for the advice Peter, that's what I do in general terms, what I'm missing is the grease cleaning bit but I'll try that next time. That Y screw nut adjustment is a pain, it has to be checked at several points along its run. And next time I do that seriously I'll think of inserting a few retention washers while I'm at it.
Talking privately to someone else from here the impression I got was that the saying "You pay peanuts, you get monkeys" is valid but the fact remains that this is quite a substantial peanut both in capital terms and staggeringly so in time (equals money!) terms due to assembly and maintenance. Especially for me who's trying to start a business up where this CNC voodoo is paramount and here I am wasting my precious time and leaving behind other tasks equally important.
Again, I am convinced that the theoretical design of the Clockwork Orange is quite good for the spec, but production and commercially wise not quite so. I find it infuriating that having received a 4th-axis assembly it was completely jammed and I had to "open the lid, shake, and put the lid back in place" for it to work at all! Don't those people simply test their stuff before shipping out?
Oh, and give thanks for one certain representative who shall remain nameless, if it weren't for him many people me included would be left in very deep lurch.
Clockwork Orange is a S600 with 4th axis, Kress 1050. Software is UCCNC, DeskProto, Rhino, DraftSight. Also a Silhouette Cameo for vinyl, plastic card, etc.
Miguel,
I think the whole of the English speaking Stepcraft community owes a vote of thanks to the nameless one!!!!
I feel for you having to waste your precious time fettling your machine when it should be earning its keep.
Good luck with your next "Battle of the Y's"!!
Peter
SC 420/2, Industrial VFD spindle from StoneyCNC
UC100 + UCCNC
Cut2D, Autosketch10, Draftsight, Eagle 9.5.1
There is no problem, however simple, that cannot be made more complicated by thinking about it.

Clockwork Orange is a S600 with 4th axis, Kress 1050. Software is UCCNC, DeskProto, Rhino, DraftSight. Also a Silhouette Cameo for vinyl, plastic card, etc.
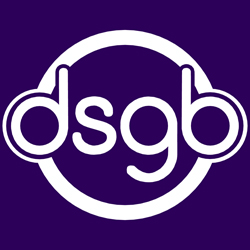
I like peanuts. Well, peanut butter anyway. I reckon Stepcraft is more Nutella, or perhaps peanut butter with palm oil (which I dislike) rather than peanut oil.
Meanwhile back at the ranch, I received the promised small industrial quality spindle from Rory today. It looks great but I have no power supply cable or time to test it until at least Tuesday next week.
Here is a short video of me jog testing all three axes with it fitted. It weighs 1.5 kg and stickout is 30 mm below the base plate.
http://www.youtube.com/watch?v=j5hxx007h6Y
Doug
Stepcraft 2/840, StoneyCNC industrial HF spindle, 4th axis, TurboCAD 2016 Professional 64 bit, MeshCAM, GWizard feeds & speeds calculator, UCCNC
Hobby use: guitar building (luthiery), https://dsgb.net
I got the impression from StoneyCNC that my troubles were to be expected because of the entry level of the 'hobby' machine. I build ukulele fora living and my entry level instrument costs £425... a little bit different to the near £2000 I paid for my 600 which after 2 days of assembly and reassembly twice I still cannot get to work. My customers get a replacement if they are dissatisfied regardless of them spending £425 or £2500... I am very frustrated that the support always defers to advice to watch the assembly videos with the implication that you haven't done it right so try again. I am to say the least disillusioned and disappointed with the machine and supplier.
- 44 Foren
- 7,336 Themen
- 63.2 K Beiträge
- 6 Online
- 26.3 K Mitglieder