Hints for drilling
Hi,
my name is Federico. I have an 840v2 with a kress 800 fme mill. I would like to build a new spoil board for it. It will be a MDF plate, 19 mm thick with 83 holes where I will screw m6 threaded inserts.
Each insert requires an 8mm hole through the mdf.
Is it better to drill each hole vertically with an 8mm drill bit (the kress spins at minimum 10.000 rpm) or a spiral cut with a 4mm or 6 mm end mill?
Thank you in advance!
Federico
hi,
i prefer milling these holes and not drilling. using an 8 mm diameter drill bit causes bigger forces and you have to slow down the rotation speed.
the next point is: you need a thicker victim plate. the 8 mm drill bit with the usual 120° peak needs at least 3,5 mm more drilling depth to get through.
did you measure the length of you drill bit? i guess this can cause the next problem.
Andreas
I have been drilling /milling 1/4" (6.35mm) holes in 10mm beech. A technique that seems to work well is to drill a pilot hole of 2mm, and follow this up with a 1/4" end mill.
The 2mm hole is set to only just touch the spoil board underneath but allows the end mill to operate correctly. Holes are spot on size wise, i.e. 0.250" -0.000" + 0.002".
SC 420/2, Industrial VFD spindle from StoneyCNC
UC100 + UCCNC
Cut2D, Autosketch10, Draftsight, Eagle 9.5.1
There is no problem, however simple, that cannot be made more complicated by thinking about it.
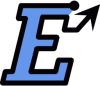
Hi,
milling will work much better than drilling.
Even the slowest rpm of a Kress is usually much too fast for a 8mm drill bit -> it will get too hot, burn your mdf and wear out pretty fast.
Christian
Ok, thank you all for the help! I will go the milling route.
Any advice on the optimal diameter for the end mill? is 6mm too big for spiral cutting an 8mm hole?
Federico
Hi Nitro24,
With 84 holes to drill / mill, treat yourself to an 8mm end mill if you can find a collet to match for your spindle. Otherwise the spiral / stepped approach will work fine with a 6mm (or even smaller) end mill.
Make sure to keep the holes clear of chips - otherwise you will be replicating the pre-historic way of making fire!!
Peter
SC 420/2, Industrial VFD spindle from StoneyCNC
UC100 + UCCNC
Cut2D, Autosketch10, Draftsight, Eagle 9.5.1
There is no problem, however simple, that cannot be made more complicated by thinking about it.
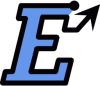
Hi,
- 4 to 6mm is perfect (1/2 to 3/4 hole diameter).
- Less than half hole diameter is OK, too but takes longer to machine.
- Significantly larger than 3/4 creates more heat and can cause problems with chip removal.
Christian
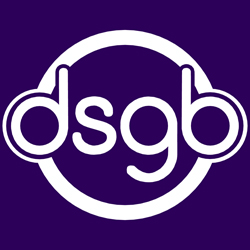
I have been experiencing intermittent issues when drilling. I share the experience here to help others avoid the same issues or offer some tips to explain what is wrong.
Some of the cuts I am doing are two-sided. I use MeshCAM to create the toolpaths which has a two sided cut ("flip job") option. To achieve this, I first drill two holes centered on the Y axis of the stock towards the ends I then fit 4 mm registration dowels to aid precise placement when the stock is flipped over front to back along the Y axis on completion of milling the top side. The stock is attached securely to a 12 mm MDF spoil board with double sided carpet tape positioned to avoid the drilling region.
Last week I successfully milled a small oak insert for my guitar design from 19 mm thick European oak. I set up the job with two 4 mm wide supports located at the top of the geometry.
My parameters are summarised as follows:
- 4 mm solid carbide four flute end mill
- Plunge speed 90 mm/min.
- Retract speed 120 mm/min.
- 5,000 rpm rotation speed (25% on Stepcraft HF500 control unit, i.e. slowest possible speed).
The drill process I use is to drill at successively deeper 5 mm depths with full retracts each time, so:
0.1 to 5 mm at 90 mm/min.
Full retract at 120 mm/min.
0.1 to 10 mm at 90 mm/min.
Full retract at 120 mm/min.
Final drill is 5 mm into the MDF spoil board so 24 mm depth in total.
On my third attempt to cut a revised design block, the bit stalled, caused the two halves of spindle body to unscrew from each other and caused a failure of the power supply in the Stepcraft HF control box (the second failure since I have had the machine in operation). This will be returned to the supplier for a replacement Kress spindle and refund of the difference. The Stepcraft spindle system does not appear to have any thermal or current overload protection, either via user replaceable fast rupture fuse or user resettable relay. This is unacceptable on any spindle, let alone an outfit costing £500. Thanks once again to Rory for a fantastic response.
My MDF is flat and secured across the entire area with double sided carpet tape.
The machine is perfectly mechanically tuned.
The router bit is relatively new and not blunt (still cuts my skin if I'm not careful). 😉
The failures cause a small amount of looseness to appear in the XZ module which then requires some more mechanical tuning. I dismantled the XZ module and extrusions yesterday to rectify a faulty limit switch (see previous post). When I reassembled it there was no looseness so no lasting damage or movement had been done.
Going forward, I will check the vertical level of the Z extrusion relative to the bed in case it is trying to drill at a slight angle.
Other than that, I conclude that the HF spindle system is not suitable for vertical drilling, even using relatively conservative parameters.
Doug
Stepcraft 2/840, StoneyCNC industrial HF spindle, 4th axis, TurboCAD 2016 Professional 64 bit, MeshCAM, GWizard feeds & speeds calculator, UCCNC
Hobby use: guitar building (luthiery), https://dsgb.net
- 44 Foren
- 7,436 Themen
- 63.4 K Beiträge
- 2 Online
- 26.5 K Mitglieder