Little drills on an aluminum plate?
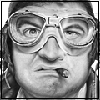
Hello,
I usually work on plastic material so I have no experience about alu.
I have to make some drills across a 100x60 mm plate made of "soft" alu (6060 type). The thickness of the plate is 5 mm and I want to make a 3mm dia hole across it. Any idea about what rpm and plunge rate should I use?
What I have available on my table:
- one 2mm solid tungsten carbide drill-bit from cnc-plus.de
- one 3mm solid tungsten carbide drill-bit from cnc-plus.de
- one steppi with HF500 spindle
I would use the 2mm bit to make a spot on the surface and then drill with the 3 mm drill-bit. But no idea about what parameters I have to use in my peek-cycle... 😳 😳 😳
Any idea?
SC300 + Spindle HF500 + Portalerhöhung + LinuxCNC + gsimple
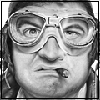
Ok, no answers in the last 50 minutes, so I decided to go by myself 😆
Step 1 - 2mm spot
I have created a 2mm deep "spot" for successive drills. I have repeated this drill operation 3 times to minimize bad-centering 'cause of the tool deflection. Here the gcode fragment:
S5000 M03 G83 R1.5 Z-2. Q0.2 F60.
Step 2 - 2.5mm drills
Here I have proceeded step by step, before 3 mm deeo, after 4mm, after 5.5 and after 6.5. But I think one can go through the material using just one peek cycle. Vibrations arises only after 4mm deep, but they are tolerable in any case.
S5000 M03 G83 R1.5 Z-6.5 Q0.2 F60.
Step 3 - 3 mm final drill
here the gcode fragment:
S5700 M03 G83 R1.5 Z-6.5 Q0.3 F60.
(deep is 6.5 mm 'cause I want to be sure I pass through the material)
I tested the 3mm drill with lower speed (bigger diameter = lower speed of the spindle) but boys.. a lot of vibrations! I think not enough torque is the reason, so the spindle was close to stop. I have increased the speed to 5700 and has worked. But the rate of vibration is much higher than with the 2.5 mm hole. In comparison the 2.5 drill was cutting butter.
Final note
I'm not a master of alu, so take my experiment for what they are: experiments! 🙂
Anyway the final diameter is 3.07 mm, not so bad for a router!
Off-topic:
now it would be fine if I could create an M3 thread on a 2.5 mm hole. Are manual tool existing for this kind of operation?
SC300 + Spindle HF500 + Portalerhöhung + LinuxCNC + gsimple
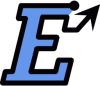

Hi Julius,
Thanks for your experiments - vey helpful. For taps and dies this company is very hard to beat - http://www.tracytools.com
I'm sure you know this but if you make a block drilled for good fit for the tap you will tap the hole perpendicular. Be very careful as you tap the hole as small taps are very easy to brake and very difficult to get out
Here's a couple of guides I made on a lathe but the would be equally well made on the Steppi now you can drill alloy
Have fun!
SC840, HF500, UCNNC, Vcarve Pro, Turbo Cad

Hi Julius,
Thanks for your experiments - vey helpful. For taps and dies this company is very hard to beat - http://www.tracytools.com
I'm sure you know this but if you make a block drilled for good fit for the tap you will tap the hole perpendicular. Be very careful as you tap the hole as small taps are very easy to brake and very difficult to get out
Here's a couple of guides I made on a lathe but the would be equally well made on the Steppi now you can drill alloy
Have fun!
SC840, HF500, UCNNC, Vcarve Pro, Turbo Cad
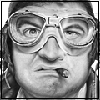
Thanks for the photos.
I never made milling on alu, so I was quite skeptic about this possibility for the Steppi. I'm using gsimple as primitive/cheap cad-cam solution, but it offers helical-milling too, so I will give it a try.
Now I have to buy/order a 2mm endmill and make some other attempts.
Honestly my impression is that a 2,5mm hole is the maximum diameter for a machine like the Steppie. With the 3 mm hole I strongly suspect that I was largely beyond that limit.
thanks for the link, I was searching for something exactly like that.
I hope that I will able enough to make a perpendicular thread even manually!
Service information:
Unfortunately my boss (wife) said that we have to go on holidays (that is an order).
So I will be able to report you my results only at the beginning of next July... 🙁
SC300 + Spindle HF500 + Portalerhöhung + LinuxCNC + gsimple

Can't you take the 300 with you?
Happy holiday!
SC840, HF500, UCNNC, Vcarve Pro, Turbo Cad
hi.
forget to mill/work aluminium/brass any metal.the machine can not do these jobs
If you can not do it, this does not mean the Maschine can not do it.
Just try a litle bit harder...
Soft metals like alu etc. Are no Problem for experienced users of Stepcraft. :woohoo:
i have 5 machines in my shop.i work aluminium,brass abs,steel.
the only machine that can not work is the stepcraft
Are you shure you perform right?
Maybe you have to check something, to get the whole out of your CNC.
5 other machines:
4 drillingmachines
1 sandingmachine
???
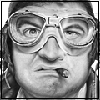
hi.
forget to mill/work aluminium/brass any metal.the machine can not do these jobs
I'm back from from holidays, endlich! 🙂 :side:
@PERANDIN
Well, somebody else has done some good job on alu with the Steppi with no big problems. If you search on the forum you can find some examples.
I agree with you that the Stepcraft is not recommended for this kind of things, but if you have to do just one or two pieces then (with big patience) you can do it (IMHO).
SC300 + Spindle HF500 + Portalerhöhung + LinuxCNC + gsimple
I have milled and drilled al. plate to make a cover plate for a water outlet on an old MG, using my stepcraft machine.
I use fusion 360, peck drill and use a very shallow depth of cut, along with WD40 spray during the operation.
It takes a while, but it can be done.
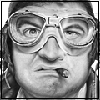
coanda, what is a "fusion 360, peck drill" exactly? A drill bit or what?
SC300 + Spindle HF500 + Portalerhöhung + LinuxCNC + gsimple
coanda, what is a "fusion 360, peck drill" exactly? A drill bit or what?
fusion 360 >> CAD Software
peck drill >>> The drill hole depth is drilled in several passes.
- 44 Foren
- 7,436 Themen
- 63.4 K Beiträge
- 4 Online
- 26.5 K Mitglieder