Machining mdf and plywood. How easy or hard is?

Hi all!
I would like to know what sizes of materials are you using with your stepcraft without problems. I am so confused about the stepcrafts capabilities so much that i canot deside if its good to work with. What are your experiences with these materials and what are your most useful bits for routing/carving? Have you any tip to suggest for not spending a ton of moneys but actual be able to work smooth? For now the thing i keep in mind is that is better to work with parallel version and with a good controler software. But how easy or hard is that i canot know. Have any of you worked with a setup like that and the tool length sensor? I want to make some works with the stepcraft but im stuck with things i have read for difficulties with the machine, building or operating. I am not an owner but im planning to become one. Could you rate how easy or hard is the whole operation for a total newbie in the field?
Thank you in advance!
Nick
There are threads in this forum where people write about their experience. My experience is also all here, if I do something new, I`ll make a post. This forum, youtube etc should give you some idea about the capabilities. I have machined sheet balsa and plywood up to 4mm thick, but it is difficult to comment because there are different grades of plywood. Poplar is easy to machine, but modelbuilding multilayer Baltic Birch plywood might not be so. People have different expectations so what works for me might be considered insufficient by someone else.
Building and flying model airplanes is my main hobby, that is why I don`t use my Stepcraft very often. I have about 150min of total cutting time. I had some difficulties at the beginning, but now it is a tool I can depend on. When I need something I make it and part dimensions are as needed. I am very happy with the machine, I just hope it lasts.
Stepcraft 600SF (version 1) parallel port
Proxxon IBS/E
Mach3
devCad Cam Pro; devWing Cam; devFus Cam; Profili Pro 2
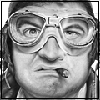
Hi Nick,
I think that the most difficult thing is... the technical jargon. When I started I had no idea at all of what a simple sentence like "jogging the X axis" means. :blush:
Take in account long sessions of testing to understand what is the best speed (feed rate) the best deep of cut (DOC) with the best tool (end mill). It will take some time, but by googling you can find a lot of info.
Mounting the machine is not so hard, I think that the software part is the one more complicated. I mean, I have no idea if you want to make complex 3D parts or simple 2D (or 2.5D) shapes like me. If so, I think that in max 3 weeks you can became an expert.
SC300 + Spindle HF500 + Portalerhöhung + LinuxCNC + gsimple

Thank you for your answers friends!
I hope to be easy to asembly the machine! Offcource i need to learn the jargo 🙂
The things i want to make are simply and complex wooden reliefs and 3d carved items. I like that the 840 have a decent size, so i could create 2 or more items at once. I suppose that i have to go with soft woods, because i think the stepmotors are too weak, but i like that the machine seems to have good quality so maybe i give a try. The forum here has a lot of informations but the most of them are german language and isn so easy to me to understand. Also the video tutorials from the company have not english subtitles and i feel that the machine is directed for deutchland people most, maybe i am wrong but thats what it seems to be real. At the same prices there are chinese machines a lot stronger than stepcraft but i believe i would have more troubles than gains and no support, and because that i m searching here and asking for infos for stepcraft.
Maybe if i buy stepcraft i have to upgrade steppermotors to something stronger. If i can frase wood at 2-3mm (or more) per pass with stepcraft i think its ok for me. But if i have to take 0.5 passes this is so slow for real work. On a video they talked for 840 and says that is more for commercial purposes not only hobby use. I know that there is try and fail but if its for your work you have to minimize fails, also you cant go with cheep quality machines, and you pay not only for the machine you get but also for the companys support you get.
Sorry for the big text
Nick

I cut birch wood with 2mm per pass and I only have a SC1 with a Proxxon spindle.
And of course there are currently more german speaking users, because the machine is available here for nearly 2 years. I guess with the worldwide kickstarter campaign this will change soon.
SC 420 mit DIY parallel + Proxxon mit Mod + HF500 + SprintLayout + LibreCAD/QCAD + FreeCAD +WinPC starter/USB->EstlCAM + EstlCAM LPTAdapter + EstlCAM Handrad + DIY Vakuumtisch
Gruß, Andreas

Nick you don't need stronger stepper motors - all they are doing is moving the portal around (that holds the spindle/drill). I saw a post somewhere that made a lot of sense - stronger motors might destroy your machine if you have a crash, whereas the motors that are supplied will just stall.
It's the high speed of your router bit that allows it to cut easily. A rule of thumb is to have a depth of cut that is half the diameter of your cutting bit, thus a 6mm bit will happily cut 3mm passes but a 1mm bit would probably snap if you tried 3mm passes.
I cut birch plywood, solid oak, elm, ash, beech - no problem with any of them using the "pass depth is half diameter" rule - up to 6mm bits with a Stepcraft HF350 spindle.
It is vitally important to securely clamp your work piece. On my SC600 I had a piece of plywood that wasn't clamped tight enough and the step motors were strong enough to pull it out of the clamps and haul it down the table.
Donald
Learning from mistakes until I become an expert!

Friends your answers are so helpful for me! Thank you a lot!
Another thing i would like to know is what speeds do you use for you spindle. I reed some things and seems to depend not only on the procesed material, but also to the bit size. Do you recomend me to go with the proxxon spindle for these materials? I have looked for kress 1050 which is two versions one at 5000-25000rpm and other at 10000-32000rpm. What do you think is most suitable?
Nick
- 44 Foren
- 7,436 Themen
- 63.4 K Beiträge
- 3 Online
- 26.5 K Mitglieder