Z-Achse senkrecht ausrichten
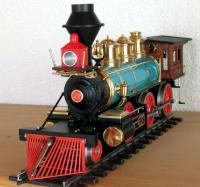
Hallo Wolfgang,
die Pulverbeschichtung ist in der Tat ein Problem für die Genauigkeit in diesem Bereich. Bei meiner Spindelaufnahme habe ich die komplette Farbe von den wichtigen Flächen abgeschabt. Wenn du willst kannst du dir eine neue Halteplatte für die Spindel aus 10mm Alu ausfräsen und dann hast du diese Problemstelle beseitigt und kannst die Spindel immer senkrecht montieren. DXF Pläne dazu gibt es hier im Forum.
Alle anderen Stellen der Fräse zu entlacken wird nicht viel bringen denn die Teile werden einmal ausgerichtet und festgeschraubt. Danach brauchen sie eigentlich nicht mehr zerlegt werden, im Gegensatz zur Spindel die man doch öfters aus der Halterung entnehmen muss.
Gruß
Helmut

Abhilfe bringt eigentlich nur eine neue fräse und diese im Rohzustand lassen bzw. könnte ich sie einfach Sandstrahlen in meiner Box. Am einfachsten wäre es von der ganzen Maschine die Beschichtung zu entfernen und das Alu pur lassen .. :unsure:
Moin,
Du sprichst mir aus der Seele! Schon vor Monaten - als "Old-Opa" seine Aufbauerfahrungen hier mitteilte und davon schrieb, wie oft er die Beschichtung entfernen musste - habe ich in diesem Forum einen Beitrag geschrieben (gerichtet an "PU"), ob man die Stepcraft nicht vielleicht auch OHNE Beschichtung, also in Alu pur, bekommen könnte.
Ich erntete mehr oder weniger unsachliche Antworten ... z. Bsp.: ... die sieht doch so viel schicker aus.
Dieser Beschichtungskram sieht vielleicht ganz gut aus, gibt auch ein unverwechselbares Marken-Image her, ist aber nicht förderlich für zielgerichtete Modifikationen hinsichtlich Vermessung und anderer Aufgaben.
Gruss
Gruss Michael
begonnen mit 420/2, Alu-Fräse "KARLA" (noch im Bau)
EstlCam mit Arduino NANO, WinPC-NC USB
Kress, QCAD, Fusion 360, Inventor, Winghelper
Moin,
Ich habe mir die Aufnahme jetzt mal genauer angesehen, wenn ich die Spindel hineinstelle, sollte man annehmen dass die abgesetzte Fläche eben auf der Aufnahme aufliegt. Leider ist dies nicht so, da die Beschichtung unterschiedlich hoch ist, siehe auch die Antwort zu der Materialstärke der Aufnahme (+/-0,2mm). Ich denke da kann ich davon ausgehen dass die Spindel nicht senkrecht nach unten zeigt. Abhilfe bringt eigentlich nur eine neue fräse und diese im Rohzustand lassen bzw. könnte ich sie einfach Sandstrahlen in meiner Box. Am einfachsten wäre es von der ganzen Maschine die Beschichtung zu entfernen und das Alu pur lassen .. :unsure:
Das würde pur belassen würde auch nicht helfen. Denn die Materialstärke ist nicht ausschlaggebend für die senkrechte Ausrichtung nach unten. Ok, zugegeben, ich könnt wieder eine Zeichnung machen und zeigen, das dabei sogar der Hunderstel unterschritten würde, aber ich glaube, das brauch ich nicht.
Viel wichtiger ist:
Die Aufnahmebohrung und die ist konisch...
...und das liegt nicht an der Pulverbeschichung, sondern am Fertigungsverfahren. So, wie die Spuren aussehen, tip ich auch einen Laser und der war falsch eingestellt. Beim Laserschneiden muss der Focus auf die Mitte des Materials eingstellt werden und nicht auf die Oberfläche.
Allerdings könnten die Teile auch mit einem Plasmabrenner hergestellt sein, aber dann... na ja.
Ich hab meine neue Aufnahme für die Kress extra ab- und ausdrehen lassen, damit Aufnahmebohrung und Anschraubfläche auch wirklich senkrecht aufeinander stehen.
Aber schön zu sehen, wie um den heißen Brei gerannt wird. Das Wippen bekommt eben nur weg, wenn man die Teile 48 und 50 einschleift, sprich das Axialspiel entfernt.
Trotzdem, ist halt eine "Käsefräse" ...
sswjs, aka Jens

... hast Du nun eine Stepcraft und hast Du sie selber zusammengebaut? Von Dir hätte ich nun nicht erwartet, dass Du das nicht weisst ...
Was meinst Du nun genau damit? :silly:
Ob ich noch weiß ob ich eine SC habe oder ob ich nicht mehr weiß das ich sie selber zusammengebaut habe?
Nein - ich habe keine SC! Aufgrund von mir nicht zur Verfügung stehende "Hands on experience" und in Ermangelung einer nicht vorliegenden Aussagekräftigen Dokumentation suche ich mir oft mühselig die Basisinformationen zusammen wie in diesem von Dir kommentierten Beitrag.
Das solche Fragen von mir sich teilweise recht naiv anhören kann ich mir gut vorstellen - vielleicht sollte ich es doch lieber lassen ...
It's not only about tools it's also about skills!
...und das liegt nicht an der Pulverbeschichung, sondern am Fertigungsverfahren. So, wie die Spuren aussehen, tip ich auch einen Laser und der war falsch eingestellt. Beim Laserschneiden muss der Focus auf die Mitte des Materials eingstellt werden und nicht auf die Oberfläche.
dat mit dem laser einstellen auf die mitte hilft dir auch nicht weiter, dann bekommste genau genommen nen doppelkonus mit der geringesten weite bei der materialstärke.
das "problem" soweit es wirklich eins ist bekommste nur weg, so wie du es beschriebne hast.
aber:
diese werkzeugaufnahme wird nach dem einsetzen des werkzeuges (spindel oder was man auch immer verwenden will) durhc die schraube verspannt, ausserdem ist sowieso eine gewisse ungenauigkeit -sprich luft -nötig, sonst bekommste garkein werkzeug rein!
ich denke auch dass sich das ganze überhaupt nicht auswirkt, solange die verspannung nicht so groß wird dass die spindel aus dem rchten winkel zur aufnahemfläche gedrückt wird.
womit wir wieder bei der materialtoleranz und der unterschiedlich dicken beschichtung sind!
Andreas
Moin,
Ok, das wird jetzt Offtopic
Das solche Fragen von mir sich teilweise recht naiv anhören kann ich mir gut vorstellen - vielleicht sollte ich es doch lieber lassen ...
Das tun sie nicht, wenn man weiß, daß du keine Stepcraft hast.
Unsere Vorstellungen beinflussen immer unsere Aussagen. Deswegen geht hier jeder hier im davon aus, du hast eine Stepcraft. Es sei denn du weist immer explizit darauf hin, du hast keine.
Das kannst du übrigens sehr schön an den Beiträgen von Christian Knüll sehen, daß er ständig darauf hinweist.
/Offtopic
Was meinte immer mein Philosophie Lehrer:
Unsere Vorstellungen und Überzeugungen sind die Grenzen dessen, was wir zu denken vermögen.
sswjs, aka Jens
PS: Du darfst mich ruhig nach technischen Details fragen.

PS: Du darfst mich ruhig nach technischen Details fragen.
Werde ich gegebenenfalls mal drauf zurückkommen ...
It's not only about tools it's also about skills!

Danke fürs verifizieren!
Auch sonst stimme ich Euch zu das es eigentlich nur eine Notlösung sein kann/sollte.
Mit Paszscheiben bekommt man z.B. das Problem des "Kippelns".
Das denke ich weniger. Wenn ich die Schrauben mit den unter gelegten Passscheiben genauso fest wie ohne anziehen kann wird sich dies meines Erachtens weder positiv noch negativ auf eine "Kippeligkeit" auswirken. Rein theoretisch ...
In der Fräserspitze findet man die Summe aller Toleranzen, vor allem die Verbindung zwischen Aufnahme und Z-Führung. Um das auszugleichen müßte man eine justierbare Aufnahme haben, oder aber die Aufnahme in der Maschine überfräsen.
Mit dieser Aussage von eon16 möchte ich meine persönliche Konklusion mal Kund tun:
Mein genannter Lösungsvorschlag mit den Passscheiben (wusste nicht mehr wie die Dinger heißen ;-)) kann immer nur eine Notlösung sein.
Maschinenteile nach fräsen / nach bohren / Passschleifen blablabla denke ich gehört nicht adressiert an Ottonormalverbraucher Kunden Hände.
Mein Verständnis Problem liegt im Folgenden (meine Maschinenbauzeiten liegen nun doch schon etwas zurück - sind aber noch nicht ganz verblichen):
Ich kenne es eigentlich nur so das Maschinenbautoleranzen - welche auch immer - kaum zu vermeiden oder sogar erwünscht sind.
Ist also Ok!
Eine Toleranzangabe sagt allerdings auch "zwingend" aus das solange ich mich innerhalb der Toleranz befinde alles wie geplant/gewünscht funktioniert.
Wenn sich aber, wie es scheinbar hier der Fall ist, die Summe aller Toleranzen negativ auf ein entscheidendes Bauteil (Z-Achse/Winkel/Ausrichtung) auswirken dann sollte Herstellerseitig über eine Lösung nachgedacht werden wie dieses wieder abgefangen werden kann. Dies wäre - wie eon16 bereits sagte - durch eine justierbare Spindelaufnahme machbar.
Andere Vorgehensweisen wie: Spindel verkantet festziehen / Pi mal Daumen schleifen bis es passt / Unterlegscheiben einsetzen wo es eigentlich keine geben sollte oder alles wieder demontieren/montieren kann ich persönlich nur als Notlösung ansehen.
Machbar - sicher - aber trotzdem Notlösung!
Just my two cents!
P.s.: Vorausgesetzt habe ich bei diesen Gedanken natürlich das die SC 100%tig innerhalb der vorgegebene Toleranzen gefertigt und dann auch zusammengebaut wurde. B)
It's not only about tools it's also about skills!
um mal aufzuzeigen, dass das mit der passscheibe schwachsinn ist folgende skizze:
schiieete. in dieser bildgrösse sieht man nicht viel. das eigentliche 8 mm loch wird mit der passscheibenllösung zwar im bohrgrund auch durchmesser 8 mm , aber beim werkzeugeintritt in den werkstoff wird es ein oval mit der langseite von 8,79 mm.
Andreas
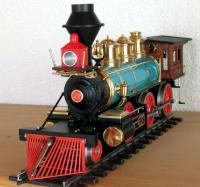
Hallo,
endlich hat sich mal jemand (drilldevil) die Mühe gemacht und das Problem verständlich in einer Zeichnung dargestellt.
Paßscheiben wären nur sinnvoll wenn die untere Seite der Z-Achse schräg abgeschnitten wäre, was aber in der Praxis kaum vorkommen dürfte.
Eine verdrehte Montage der Z-Achse ist aber durchaus möglich da die Schaubenlöcher in den Wangen etwas Spiel haben und daher die Z-Achse bei der Montage eigentlich mit einem Winkel ausgerichtet werden sollte bevor sie festgeschraubt wird. :whistle:
Die Platte mit der "komischen" Bohrung für die Spindelaufnahme könnte man sich bei Bedarf neu anfertigen oder evtl. nacharbeiten (z.B. Bohrung mit Wohlhaupter ausspindeln und evtl. Buchse einsetzen).
Eigentlich wollte ich nach der Montage die Geometrie der SC überprüfen und ggf. ausrichten, aber dafür fehlt mir ein größerer und entsprechend genauer Winkel. Daher ist dieser Punkt immer noch offen.
Gruß
Helmut
Moin,
was ich noch bemerken wollte: Aus einer E-Mail an mich geht hervor, daß sich Stepcraft um wirklich rechtwinklige Profilschnitte bemüht. Deswegen kann hier (bei der Z-Achse), ein Herstellerfehler (fast) ausgeschlossen werden.
sswjs, aka Jens

Hallo liebe Mitglieder,
Ich würde mir gern eine Spindelhalterung nach meinen Vorstellungen für die SC und der HF selber fräsen und bin dabei auf diesen Thread gestoßen.
Nun, Alu ist ja nicht gleich Alu und daher die Frage an die, die sich schon eine Aufnahme selbst gefräst haben. "Welches Alu habt Ihr verwendet, mit welchem Fräser und mit welchen Daten wie Geschwindigekeit, Einstechgeschwindigkeit, Vorschub etc. seit Ihr gefahren?
Freue mich schon jetzt von euch zuhören und werde das Endergebnis dann auch gern Präsentieren
Liebe Grüße
Hubert S.
Gut Ding brauch Weile, aber Hauptsache es geht schnell
Viele Grüße
Hubi

Da ja leider noch keine Antwort kam, habe ich mich mal schlau gemacht. Das Material ist ALMg3 :whistle:
Liebe Grüße
Hubert S.
Gut Ding brauch Weile, aber Hauptsache es geht schnell
Viele Grüße
Hubi

Moin Hubert,
AlMg3 ist nun gerade nicht so toll zerspanbar.
Sehr gut zerspanbar sind:
- AlCuMgPB
- AlCuBiPb
gut zerspanbar (u.a. und leicht erhältlich):
- AlMg4,5Mn
(entnommen einer Tabelle, die MaglO2 in diesem Forum mal veröffentlicht hat)
Im übrigen findest Du viele Infos über Materialien und Fräsparameter im von Speedo hervorragend betreuten CNC-Wiki
Gruss
Gruss Michael
begonnen mit 420/2, Alu-Fräse "KARLA" (noch im Bau)
EstlCam mit Arduino NANO, WinPC-NC USB
Kress, QCAD, Fusion 360, Inventor, Winghelper
Moin,
Nun, Alu ist ja nicht gleich Alu und daher die Frage an die, die sich schon eine Aufnahme selbst gefräst haben. "Welches Alu habt Ihr verwendet, mit welchem Fräser und mit welchen Daten wie Geschwindigekeit, Einstechgeschwindigkeit, Vorschub etc. seit Ihr gefahren?
Kein Problem, hier meine Daten:
Material: AlMg4,5Mn, 10mm plangefräst
Spindel: Kress FME 1050
Fräser VHM 3mm Fisch
Drehzahl: 29000 U/min
Vorschub: 10 mm/sek
Zustellung: 1 mm
Viel Spass beim Selberfräsen
sswjs, aka Jens
- 44 Foren
- 7,415 Themen
- 63.4 K Beiträge
- 2 Online
- 26.5 K Mitglieder