...dickes Dankeschön an das Stepcraft-Team
Einen schönen guten Abend!
Als Neuankömmling und Anfänger im CNC Bereich habe ich lange mit mir gerungen, ob ich den Schritt in diese riesig kreative Welt wagen soll.
Nach Erstbesuch in Menden, einer tollen Beratung und Vorführung durch den "Moderator" und zahllosen Recherchen habe ich es dann gewagt. Mitte August habe ich die Stepcraft 420/2 bestellt.
Glücklicherweise haben die Geräte Lieferzeiten! Nach 2,5 Wochen konnte ich den Bausatz abholen, heute kam die HF Spindel. Warum glücklicherweise:
es bleibt Zeit, in Ruhe aufzubauen, sich in die komplexe Thematik einzuarbeiten und "trocken zu üben".
Ziel für mich ist die Holz- und Aluverarbeitung, vor allem aber das Platine Isolationsfräsen. In den "Wartewochen" habe ich mich mittels des einschlägig bekannten Buches, dieses forums und einiger Tips von Gunther57 vorbereitet.
Heute dann Stunde der Wahrheit:
1. Projekt: Tonarmausleger für ein Masselaufwerk. Mit Frontdesigner und Weiterverarbeitung in Esticam habe ich die Maschine direkt mittels eines 2mm Fräsers auf POM Material "losgelassen".
Ergebnis: Perfekte Fräsung, kein Fräserbruch, sofortige problemlose Montage auf das MAsselaufwerk
2. Projekt: komplexe Arduinoplatine von Gunther als Probeprojekt eingestellt.
Erster Versuch mit 36 Gard Stichel: etwas zu tief, daher etwas Leiterbahnverlust. Da habe ich händisch im M31 Makro den Werkzeuglängensensor
um 0,05mm korrigiert und
zweiter Versuch:
nahezu perfekte Platine incl. Bohrungen!!!!! Das ist ein begeisterndes Erlebnis.
Fazit:
die Stepcraft ist ein hochpräzises Werkzeug, wenn man alle Hinweise des Herstellers und des Teams sowie der Anwender berücksichtigt.
Ich habe es nicht bereut und weiss, dass das Hobby einen grossen Sprung nach vorne machen wird.
Also nochmal: es lohnt und der Gegenwert und die Präzision rechtfertigen den Preis allemal!!
Meinolf
P.S.: die bohrungen sind alle mit einem 0,8er Bohrer, da ich bei Wechselaufforderung nicht wusste, welche D-messer folgen sollte
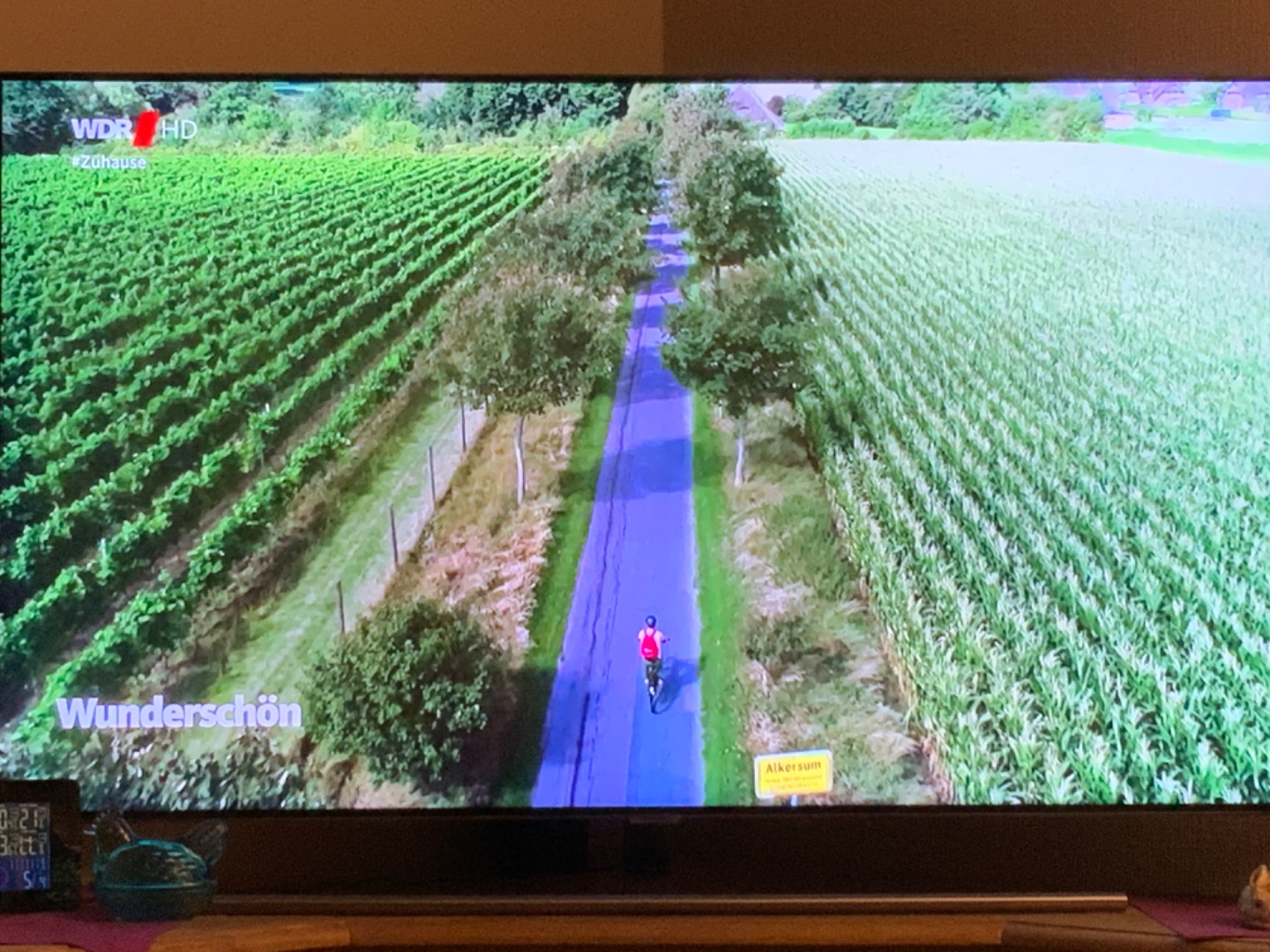
Das sieht doch Super aus
Gruß Klaus
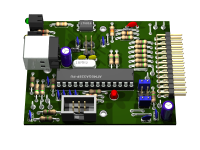
Hallo Meinolf,
also für den ersten Versuch ist das ein TOP Ergebnis! Ich hab da weitaus mehr Schrott produziert.
Aber die Frästiefe ist noch deutlich zu gross. Wie hast du den Nullpunkt gesetzt? ich verwende da eine direkte elektrische Verbindung zwischen Cu-Seite der Leiterplatte und dem Fräser. Das ist dann genauer als der WLS.
https://www.youtube.com/watch?v=rMeJiSNgCOo
Die verwendeten Bohrer stehen bei der Wechselaufforderung nochmal im G-Code. Hinter dem ersten M6-Befehl (0.9000).
M05 G00 Z30.0000 G00 X0.0000 Y0.0000 M06 T04 ; 0.9000 G01 Z0.0000 F600 M06 G00 Z2.0000 M03
Gruß Gunther
Bitte keine PN. Ich bekomme keine Benachrichtigung. Besser ein e-mail.
Hardware: SC1/300, eigenbau Aduino USB V9.6
Software: Win7-64bit, Eagle, QCAD, Freecad, Estlcam V8, V9, V10
Hobby: Elektronik
Hallo Gunther,
vielen Dank für Kompliment und die beiden Tips. Das musste ich sogleich noch mal probieren, es ist einfach faszinierend, der Maschine zu folgen.
Deshalb noch ein "gute Nacht Bild" (hatte leider noch keinen 3,2mm Bohrer bzw. 2,5mm) Deshalb nicht exakt passende grössere Bohrungen.
Aber der Rest ist ziemlich gut geworden, oder??
LG Meinolf
hi,
warum bohrst du dann mit falschem (zu grossem bohrer) nu is die platine leider schrott. irgendwie sitzen die bohrungen auch nicht wirklich mittig.
hast umkehrspiel ? überprüf das mal.
Andreas
- 44 Foren
- 7,436 Themen
- 63.4 K Beiträge
- 4 Online
- 26.5 K Mitglieder