840 almost there but white baseplate problem

Boys, boys, boys, you have to turn your Sarcasm Detectors to something above Low 👿
Clockwork Orange is a S600 with 4th axis, Kress 1050. Software is UCCNC, DeskProto, Rhino, DraftSight. Also a Silhouette Cameo for vinyl, plastic card, etc.
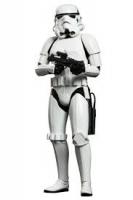
Hi,
I believe that what is needed is a quality assurance manager who will identify and collate all the various problems as they arise. Only then will the extent of these problems become clear so that targeted remedial action can be taken.
Peter
As a production engineer I think this "kit build" is a complete cop out.
Sure it saves the end user a couple of £, but not that much in the scheme of things. Sure fully assembled the shipping would be daft but the is no reason machines couldn't be shipped in two flat sub-assemblies, one for the base and the other for the gantry.
As soon as Stepcraft stand up and try to assemble these things on a proper production line then all these missing parts, ill fitting parts and bonkers design decisions will jump out at them. I'm sure a design engineer would then be called to task (or hired) to quickly put in some measures to improve things.
As sub-assemblies the fit and tuning would be SC's responsibility and we would receive tested and working machines. Quality and customer satisfaction, not to mention repeat orders would increase.
Perhaps I'm wrong but given this is V2 and all these problems exist I don't hold out much hope.
Unless changes are made I can see Chinese machines easily surpassing the quality seen here and Stepcraft will be a memory.
Owen S.
Production Engineer
HWM-Water Ltd.

As a former purchasing manager, I agree completely. I have no objection to kits, I object to bad kits.
Clockwork Orange is a S600 with 4th axis, Kress 1050. Software is UCCNC, DeskProto, Rhino, DraftSight. Also a Silhouette Cameo for vinyl, plastic card, etc.
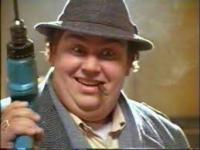
I would like to concur with the above two statements because i like Fish finger sandwiches.
I had exactly the same problems as Frank with my 840. The short cable was dealt with easily but the base-plate caused much frustration.
I managed to fit the base-plate with some force but then it proved impossible to get the y-axis to run freely. I had to sand down the edges of the base-plate. Following this I was able to tune the y-axis (after a great deal of effort, discussion with Rory and reading the many set-up related posts on this forum).
However, after a month or so of trouble free use the y-axis drive belt failed yesterday!
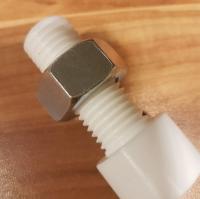
Have exactly the same problem with my 2/840 diy kit.
The depth milling is by far to less and also the width is by far to much.
🙁
CNC: Stepcraft 2/840, Kress 800-Q FME, Estlcam, Deskproto 7 Multi-Axis, Umgestiegen von WinPC NC USB v3 auf UCCNC 1.2049
3D Printer: Prusa MK3S mit MMU2S, Creality CR-10, Anycubic Photon
Hi All,
I too have issues with my 840. Got the bed in with a little force with both ends loose to give some room to move.
Then did the y axis limits with the back loose which works, but the machine will not travel completely to the front about 15mm short. Even with the front plate loose.
What is happening is the baseplate is pushing the rails outwards putting tension on the lead screws at the end causing binding.
The only way i can get the full travel is to remove the baseplate.
Machine is all working with no baseplate now and front and rear plates are tight.
Now i go to put the baseplate back in and there is no way its about 0.2-0.3mm to wide at the front to even get it started in the rails.
Any suggestions or ideas, surely i dont have to get a block and start sanding it to fit????????
Hi,
You've hit the nail on the head unfortunately!!
Get all your "tuning" done without the baseplate fitted, then "adjust" it with block and sandpaper. Don't overdo the sanding, otherwise the base might move with machining forces/vibration.
Good luck with it.
Peter
SC 420/2, Industrial VFD spindle from StoneyCNC
UC100 + UCCNC
Cut2D, Autosketch10, Draftsight, Eagle 9.5.1
There is no problem, however simple, that cannot be made more complicated by thinking about it.
- 44 Foren
- 7,436 Themen
- 63.4 K Beiträge
- 5 Online
- 26.5 K Mitglieder