Spindle / Bed Tramming (840) (Supports?)
Hello..
In the midst of assembling my 840, I started thinking a bit about the "squareness" of the machine. I also am contemplating the expanse of unsupported bed, and how much deflection will be present when cutting in the center.
Having reviewed the instructions for "linear accuracy," I find them a bit vague and inadequate. My basic plan is to run an indicator that is clamped to the spindle mount in both x/y, then adjust accordingly in the gantry. Then comes the squareness of the spindle to bed. While again possible in the gantry, that is now a 3 axis adjustment. What fun!
Then, if I wanted to really get picky, what about the alignment of the bed to the spindle travel (so as to allow repeatable jig fixtures to be exchanged and referenced using stops that are indexed on the clamping slots)... ?
Finally, the deflection question. Has anyone thought a rigid support frame? Has anyone had this issue?
I have a 620 with the aluminum t-slot machine table which gives a bit of extra stiffness. I topped it with a MDF spoil board. For repeatability in positioning, I used the machine to cut the front end of the MDF so it was parallel to the x-axis and smoothed the top with a 1/2" smoothing bit. There are several methods for how to measure the spindle (I'm going to use the Edge Technologies Mini Tram Pro), but the problem is how to tram the spindle (if it's needed). I talked to Dan at Stepcraft and he said the only method would be to shim the plate at the 3 mounting screw locations. I've purchased some M8 1-mil shim washers, but haven't yet checked the spindle - my next job.
S2/600, Industrial HF spindle (StoneyCNC)
DL445, 4th axis, touch probe, 3D probe
UC100 + UCCNC (Win10)
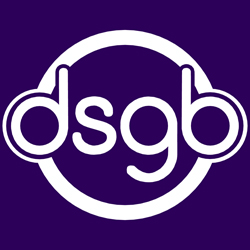
I had some issues when drilling recently (see post below):
http://www.stepcraft-systems.com/en/forum/milling/3455-hints-for-drilling#41191
So as part of the investigation, I decided to check the squareness of the Z axis to the machine bed to see if I was in fact trying to drill at a slight angle to the vertical. Actually, given that I have had successful drilling operations, this can't have been a significant contributory factor, but I decided to check in any case because I don't recall the assembly instruction manual prompting the user to check relative level of the Z axis to the machine bed.
A couple of pieces of information:
- My 2/840 machine has an aluminium T-slot bed fitted.
- All three axes are perfectly mechanically tuned.
- The X axis extrusion is aligned with the edges of the Y axis gantry supports on each side.
The first thing I did was to level the machine relative to my garage floor. This required use of a £2 coin and a 50p coin at the back left support and a £2 coin only at the rear right support.
Then I checked the level of the Z axis extrusion to find that it was noticeably off vertical. I don't have a fancy digital angle measuring device (I forgot to add this to my Christmas list!) See pictures attached. One shows the Z extrusion actual level, the second the difference between actual vertical and the Z axis extrusion and the last shows the machine bed level.
I haven't yet attempted to tilt the X axis extrusion and then tighten the fasteners to try to correct this. My thoughts are that this shouldn't really be necessary... :dry:
Doug
Stepcraft 2/840, StoneyCNC industrial HF spindle, 4th axis, TurboCAD 2016 Professional 64 bit, MeshCAM, GWizard feeds & speeds calculator, UCCNC
Hobby use: guitar building (luthiery), https://dsgb.net
The assembly instructions are unfortunately devoid of any guidance on how to ensure the spindle ends up perpendicular to the baseplate. Placement of the fixed rollers during operations 1.9 and 1.11 is a critical first step in achieving this, along with operations 3.1 and 4.1 for the gantry sides.
In addition, because of the clearances on fixing screws and the unpredictable thickness of the powder coating on most of the critical areas, even the most careful initial assembly can be sabotaged unless the coating is removed in these critical areas.
The final "tuning" of the whole machine can also play havoc with careful setup in the early stages of assembly. There are many traps for the unwary, so it is not surprising that there are many pleas for help on this forum.
IMHO what is needed is companion document to the Assembly Manual that highlights and expands on the critical assembly steps that can make or mar the accuracy and performance of the final machine.
I think that many builders, like me, know how it should be done from the start once the last screw is tightened!! 20:20 hindsight is a wonderful thing!!
Peter
SC 420/2, Industrial VFD spindle from StoneyCNC
UC100 + UCCNC
Cut2D, Autosketch10, Draftsight, Eagle 9.5.1
There is no problem, however simple, that cannot be made more complicated by thinking about it.
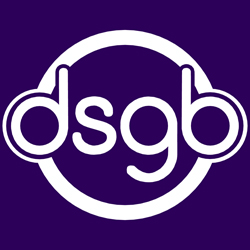
IMHO what is needed is companion document to the Assembly Manual that highlights and expands on the critical assembly steps that can make or mar the accuracy and performance of the final machine
I second that Peter. If I didn't have so many other drains on my limited free time I would happily compile such a thing. Life is tough for the one man CAD/CAM/CNC band! 🙁
Stepcraft 2/840, StoneyCNC industrial HF spindle, 4th axis, TurboCAD 2016 Professional 64 bit, MeshCAM, GWizard feeds & speeds calculator, UCCNC
Hobby use: guitar building (luthiery), https://dsgb.net
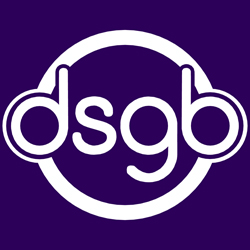
Placement of the fixed rollers during operations 1.9 and 1.11 is a critical first step in achieving this, along with operations 3.1 and 4.1 for the gantry sides
I just checked my gantry uprights and one is bang on vertical and the other a small fraction off, so that was lucky. I suppose that I will have to tilt the X axis extrusion to correct it.
Doug
Stepcraft 2/840, StoneyCNC industrial HF spindle, 4th axis, TurboCAD 2016 Professional 64 bit, MeshCAM, GWizard feeds & speeds calculator, UCCNC
Hobby use: guitar building (luthiery), https://dsgb.net
The most important thing is to know when to stop tweaking the machine and actually make something. In the early days I spent ages tweaking to the point it was almost an obsession!!
Fortunately I've cured myself of that - partly because its a real "B" to remove all the cabling so as to get at and disassemble the basics. So far no sign of wear or change needed to backlash settings (I use Castrol GTX to lubricate the leadscrews - if it's good enough for my engine!!).
Peter
SC 420/2, Industrial VFD spindle from StoneyCNC
UC100 + UCCNC
Cut2D, Autosketch10, Draftsight, Eagle 9.5.1
There is no problem, however simple, that cannot be made more complicated by thinking about it.
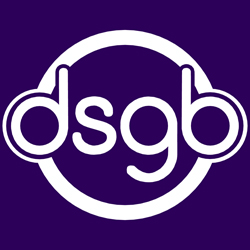
I have just completed spindle/bed tramming on my 2/840 machine. I attach a simple procedure with a few photos below.
I hope this is useful to a few people. The X axis ran perfectly at 100% on completion.
______________________________________________________________________________________
This method makes the following assumptions:
1. The machine bed is uniform and not warped. If a spoil board is fitted, it is of uniform thickness. Non-warped MDF should be o.k.
2. There is sufficient clearance (approximately 0.25 - 0.5 mm) in the X axis bearing mounting hole to move the bearing slightly in all directions. This might require the powder coating to be removed.
(a) Attach shims (of sufficient thickness to ensure that the spindle holder plate mounting screws clear the machine bed) under the spindle holder plate running back to front with double sided adhesive tape. The shims in the picture are 12" long x 1/2" wide x 1/4" thick mild steel bar. If the shims are long, it will be easier to assess the off horizontal angle of the spindle mounting plate.
(b) Traverse the XZ module to the non driven (bearing) end of the X axis extrusion as far as possible without it fouling the side of the Y axis extrusion.
(c) Loosen the screws securing the X axis extrusion to BOTH Y axis gantry uprights
(d) Drive the Z axis down to near the bed/spoil board using the software then power down the machine.
(e) Drive the Z axis down carefully by fingertips so that the shims just touch the bed/spoil board. Make adjustments so that the bearing is in the centre of the mounting hole (i.e. there is a uniform clearance all round the bearing). This should be possible to do by eye but a torch might be required.
(f) Tighten the X axis extrusion mounting screws on the gantry upright at the non driven end.
(g) Power up the machine then traverse the XZ module to the opposite side (driven end) of the X extrusion as far as possible without it fouling the side of the Y axis extrusion.
(h) Drive the Z axis down to near the bed/spoil board using the software then power down the machine.
(i) Drive the Z axis down carefully by fingertips so that the shims just touch the bed/spoil board. Check that they are flush with the bed/spoil board along their entire length).
(j) Tighten the X axis extrusion mounting screws on the gantry upright at the driven end. It is likely that there will be a small gap (around 0.5 to 1.0 mm). Take up this gap uniformly by tightening the upper and lower screw alternately in small amounts.
(k) Check that there is a small amount of free play in the X axis lead screw in the back/front (Y) and up/down (Z) directions at the non driven (bearing) end by moving it manually.
(l) Power up the machine and traverse the XZ module at successively higher speeds and check for free travel.
Stepcraft 2/840, StoneyCNC industrial HF spindle, 4th axis, TurboCAD 2016 Professional 64 bit, MeshCAM, GWizard feeds & speeds calculator, UCCNC
Hobby use: guitar building (luthiery), https://dsgb.net
- 44 Foren
- 7,424 Themen
- 63.4 K Beiträge
- 21 Online
- 26.5 K Mitglieder