The thing that grates with me is that the originator suggested cutting a flat on the ball nut to make it fit - ughh!! Milling a shallow recess in the mounting plate would seem a more rational engineering solution - more difficult though I agree....
I agree, not sure what his logic was.
Could anyone be kind enough to explain how the ends are different, and just the basic differences between a lead screw/ball screw? I'm a bit new to all this and haven't really researched that aspect so far.
I'm kind of disappointed to read about these problems when I haven't even started using my machine yet!
Peter, like you, I want to do some basic prototype PCB's and also some stuff with aluminum (or aluminium 🙂 ).
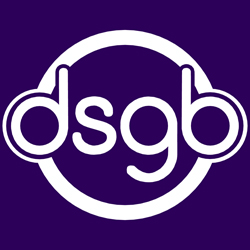
I'm interested in this modification in the longer term. I haven't even started using my machine yet though!
I could swallow a couple of hundred pounds for a significant upgrade to improve backlash and longevity.
Doug
Stepcraft 2/840, StoneyCNC industrial HF spindle, 4th axis, TurboCAD 2016 Professional 64 bit, MeshCAM, GWizard feeds & speeds calculator, UCCNC
Hobby use: guitar building (luthiery), https://dsgb.net
Hi,
Sorry - I've been a bit lax in my terminology, I written lead screw on occasions when I should have said ball screw. I think lead screw is properly applied when an Acme or similar thread is used - but I will bow the those more knowledgeable than I.
Unfortunately we cant get aluminum in the UK, all the stockists have here is alumunium so I'm stuck with that!!
On reflection, I'm 99% certain that the ball screw used is going to be a standard off the shelf item, otherwise the tooling costs would have been prohibitive for a startup enterprise. Stepcraft were after all building down to a price so as to gain a foothold in the market.
The picture in a previous link shows the FGR ball nut on a standard Stepcraft ball screw, so I think that makes it almost certain that it's a standard item. Perhaps there is someone in the know who can confirm that.
I don't at the moment see any need to go over the top with the end bearings - this is a light weight machine, so fitting double row angular contact bearings wouldn't make sense. In any case the smallest I have been able to find are 10mm id, so wouldn't be of use for a 10mm ball screw. In the event I think all the existing ball screws have 3mm ends of various lengths machined to fit ball bearings or coupling sleeves.
Peter.
SC 420/2, Industrial VFD spindle from StoneyCNC
UC100 + UCCNC
Cut2D, Autosketch10, Draftsight, Eagle 9.5.1
There is no problem, however simple, that cannot be made more complicated by thinking about it.
Unfortunately we cant get aluminum in the UK, all the stockists have here is alumunium so I'm stuck with that!!
Not to get off topic, but it was my understanding that aluminum and aluminium were the same thing, we just call it differently here and there. Am I wrong?
If we can get the parts and make the pieces etc., I'm willing to give it a try just doing a single axis, like X or Z just to see how it works. I just can't afford to spend a lot at the moment since I just got my machine and I have accessories and enclosure etc. to get.
Post back when you get the details about the cost.

Unfortunately we cant get aluminum in the UK, all the stockists have here is alumunium so I'm stuck with that!!
Not to get off topic, but it was my understanding that aluminum and aluminium were the same thing, we just call it differently here and there. Am I wrong?
No - not at all! That's the same stuff with different names. But I never heard about "alumunium". :huh:
Aluminium versus aluminum
It's not only about tools it's also about skills! 😉
OOPS!! Typos galore.
Thanks Worldhusky for that link - fascinating how some of these oddities arise.
Peter
SC 420/2, Industrial VFD spindle from StoneyCNC
UC100 + UCCNC
Cut2D, Autosketch10, Draftsight, Eagle 9.5.1
There is no problem, however simple, that cannot be made more complicated by thinking about it.
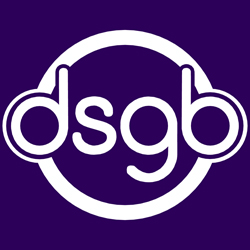
On reflection, I'm 99% certain that the ball screw used is going to be a standard off the shelf item, otherwise the tooling costs would have been prohibitive for a startup enterprise. Stepcraft were after all building down to a price so as to gain a foothold in the market.
The picture in a previous link shows the FGR ball nut on a standard Stepcraft ball screw, so I think that makes it almost certain that it's a standard item. Perhaps there is someone in the know who can confirm that.
+1. I would also be surprised if they are custom made items rather than off the shelf. They are well engineered.
Doug
Stepcraft 2/840, StoneyCNC industrial HF spindle, 4th axis, TurboCAD 2016 Professional 64 bit, MeshCAM, GWizard feeds & speeds calculator, UCCNC
Hobby use: guitar building (luthiery), https://dsgb.net
Any one know the original supplier of the ball screws that Stepcraft use?
SC 420/2, Industrial VFD spindle from StoneyCNC
UC100 + UCCNC
Cut2D, Autosketch10, Draftsight, Eagle 9.5.1
There is no problem, however simple, that cannot be made more complicated by thinking about it.
Guys - before you get carried away, on the stepcraft website, it clearly labels the item as a lead screw, not a ballscrew. The stepcraft machines would therefore not work with a ballnut, unless by absolute fluke, someone custom engineered a the stepcraft leadscrew - so that was designed to actually be a ballscrew.
I would hate for guys to waste cash fitting a custom ballnut to fit on the leadscrew, and then wonder why it ended up worse than the current arangment.
If it's worth doing, it's worth doing properly, get the ballnut matched with the ballscrew
Try Zapp automation online
R1003 C7 ballscrew
Length
300mm
R1003-300-300-C7R 1 £15.51
R1003 C7 ballscrew
Length
700mm
R1003-700-700-C7R 1 £35.31
R1003 C7 ballscrew
Length
1000mm
Grand Total (Incl.Tax) £124.03
Thanks for the Zapp link - you did me a good turn, as suitable ball nuts are on special offer there at the moment. They are specified as identical to the ones called up in this link. I've just bought a couple for X and Z axes as these are the easiest to work on.
The picture in the link shows what I believe to be an original Stepcraft ball screw (Stepcraft are as lax in their terminology as I was originally!!) with the specified nut mounted.
The adapter is no real problem provided I can persuade my lathe to cut an M18x1 thread - otherwise I will be investing in a tap of that size!
I'll update when I know if the ball nuts fit the original ball leadscrew. If it works with the originals so much the better, otherwise the screws can easily be updated with the Zapp mating parts just as you are doing. Incidentally do your quotes include machining the ends to fit existing bearings?
SC 420/2, Industrial VFD spindle from StoneyCNC
UC100 + UCCNC
Cut2D, Autosketch10, Draftsight, Eagle 9.5.1
There is no problem, however simple, that cannot be made more complicated by thinking about it.
Thanks for the Zapp link - you did me a good turn, as suitable ball nuts are on special offer there at the moment. They are specified as identical to the ones called up in this link.
Could you post a link to the specific ones you got? The Moore site gave you the choice of sealed or unsealed, wasn't sure which one to try, what did you choose?
I've just bought a couple for X and Z axes as these are the easiest to work on.
Thats great news, fingers crossed.
We purchased our Miniature ballscrew from the Uk, we had a mount like that one shown, 3dprinted out of nylon which arrived, and looks great, and fits.
The stepcraft screw, is not designed to have balls in it, so you gonna have to fork out ~200 pounds for a set of 3 custom ballscrews, and then do some DIY to get them mounted
I can post pics of our one, once we have all the bits
Sorry I didn't catch this, looking forward to seeing how it turns out.
Hi,
Here is the link to the Zapp Automation ballnuts that I have on order.
This is the best price I have seen for ball nuts anywhere and beats my quote from Moore International by almost a factor of two.
Hoping the existing ballscrews are compatible!
Peter.
SC 420/2, Industrial VFD spindle from StoneyCNC
UC100 + UCCNC
Cut2D, Autosketch10, Draftsight, Eagle 9.5.1
There is no problem, however simple, that cannot be made more complicated by thinking about it.
I'm interested in this modification in the longer term. I haven't even started using my machine yet though!
I could swallow a couple of hundred pounds for a significant upgrade to improve backlash and longevity.
Doug
I totally agree with you Doug. I will also consider to replace them if someone could find a suitable replacement 🙂
Stepcraft 2 430
Kress 800 FME
UCCNC + UC100
Cut2D Desktop
- 44 Foren
- 7,436 Themen
- 63.4 K Beiträge
- 0 Online
- 26.5 K Mitglieder