Dear user, the forum software has been updated. For the first login please reset your password.
A stupid question about end-position switches
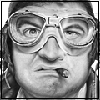
I know, maybe it's just me... but I don't understand why on my SC300 there is just one limiting switch per axis. Should not be there two switches per axis as minimum? :blush:
For example: on the Y-axis, the switch limiting the travel distance is located near the side where connectors are plugged in. But on the other side (near the emergency-stop button) there is no the same switch, why?
I'm just curious to know the reason of that...
SC300 + Spindle HF500 + Portalerhöhung + LinuxCNC + gsimple

Those switches are not for stopping a machine which runs crazy. The switching lever is anyhow too short to allow the motors to be stopped before it reaches the end.
The switches allow WinPC NC to find a fixed reference point. As a properly setup WinPC knows the size of the table, there is no reason to start a job which has a working piece that exceeds the boundaries.
SC 420 mit DIY parallel + Proxxon mit Mod + HF500 + SprintLayout + LibreCAD/QCAD + FreeCAD +WinPC starter/USB->EstlCAM + EstlCAM LPTAdapter + EstlCAM Handrad + DIY Vakuumtisch
Gruß, Andreas
Also if you work with Mach3, there is "Softlimits" which can (if enabled) prevent the machine to go over the hardware limits.
I did that and get a warning if any file would be out of (physical) boundary (setup in config).
p.s.: I set physical limits a bit lower than possible ones because I don't want my machine to reach 'physical' endpoints when working automatically. 0.5mm is enough 'safety' for me.
Frank
Steppcraft 600/2 + HF500 + SwitchBox + Laser + Schleppmesser
Absaugung und Vakuumtisch
an Mach3 oder UCCNC mit Taster für Z-Null und Werkzeuglänge

isn´t it possible to use the y axis switch e.g. for end positioning also? in winpcnc you can use the INPUT again. but is it possible is the question therefore that the 3 switches are somehow serial...
there must be a way to connect each switch seperatly. then you can use it as reference AND end switch.
but unfortunalty the cabinet has no other INPUT possibilities. there must be another cabinet. then maybe it works fine!
Gruß
Sven
Seit vierundsechzig Minuten sitzt Peter schon an einem runden Tisch in einem Besprechungszimmer und wartet. Er ist exakt vierundsechzig Minuten schlechter gelaunt als vor vierundsechzig Minuten,
SC600/I - HF500 - WinPC-NC USB + Handrad
ESTLCam - CorelDRAW X7 - Cut3D - SketchUp - LaserCAM
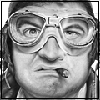
but is it possible is the question therefore that the 3 switches are somehow serial...
yes, now I realized that those 3 switches are linked together in a serial manner. So there is no way to know which one was switched on or off. I wonder how they can be used by WinPC to establish a reference point.
My question arise from what is happened to me yesterday: I was playing with LinuxCNC and jogging the axis using the keys on the keyboard (yes, like a 5-year aged child). When one axes reaches a switch then linuxCNC immediately stops working. This seems reasonable to me.
BUT, if you jog the router in the opposite direction using the keyboard then.... it reaches the end position and the motor gets not stopped(!). This means that if you keep the opportune key pressed with your finger you can even damage the motor (!!!).
So my question is still here: a good CNC machine should not have switches at both ends of every axis??? :blush:
SC300 + Spindle HF500 + Portalerhöhung + LinuxCNC + gsimple

I wonder how they can be used by WinPC to establish a reference point.
well I´m not sure about LinuxCNC as far as I´m using WinPCnc USB...
But the routine works somehow like this:
go Z reference
wait for ref switch
go back a bit (release the switch)
go X reference
wait for ref switch
go back a bit (release the switch)
go Y reference
wait for ref switch
go back a bit (release the switch)
in WinPCnc is also a feature that monitors the machine so you can not got further that the axis end pos.
Gruß
Sven
Seit vierundsechzig Minuten sitzt Peter schon an einem runden Tisch in einem Besprechungszimmer und wartet. Er ist exakt vierundsechzig Minuten schlechter gelaunt als vor vierundsechzig Minuten,
SC600/I - HF500 - WinPC-NC USB + Handrad
ESTLCam - CorelDRAW X7 - Cut3D - SketchUp - LaserCAM

Not necessarily, because you would simply not keep a key pressed.
What value do additional switches add? First of all they would increase the price tag!
I run my SC since more than a year and i do not miss an end-switch. I only miss the reference run which is not available in EstlCAM.
If you feel the strong need to add end switches on the opposite of the existing ones, feel free. Just wire them in series with the existing ones.
I don't think that the motors will be damaged if they are forced to stop because of the currency limit in the motor driver chips.
How WinPC can see wheather X,Y or Z switch has been pushed is easy: It only moves one axis at a time, so there is no way for another switched to be triggered.
SC 420 mit DIY parallel + Proxxon mit Mod + HF500 + SprintLayout + LibreCAD/QCAD + FreeCAD +WinPC starter/USB->EstlCAM + EstlCAM LPTAdapter + EstlCAM Handrad + DIY Vakuumtisch
Gruß, Andreas
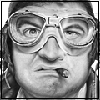
Well, you're right. Moving just one axis a time and waiting for the switch can be used to set a reference point.
Do you want to laugh? With linuxCNC when the router triggers one switch the program stops. I have to:
- turn off steppie power
- manually move the router a little back (so the switche is no more triggered)
- turn power again
Funny! 🙂
Anyway happy to know that it's not easy to damage motors when the end-position is physically reached.
Axis switches are for nothing? This can be... so why not eliminating them at all?
Yes, 3 are useful to have a reference position... but 6 switches would be better! A simple program could calculate the working area quite easily as a 3D volume using just 2 points in the 3D space.
Anyway, what above are just my speculations...
SC300 + Spindle HF500 + Portalerhöhung + LinuxCNC + gsimple

End switches are usefull in bigger machines with more powerfull motors, that can really harm the mechanical parts of the machine. But in a stepcraft the mechanical parts can withstand the stress a motor could potentially put on them, in case the user is too s.... 😆
" so why not eliminating them " ... well, that's what stepcraft did. The switches do not consequently work as end-switch. In manual mode you can easily go beyond end-point.
The switches give WinPC NC an idea of where the machine table starts and by adding the size of the table to this reference position WinPC NC also knows where the table ends. These are exactly the two points in 3D space you talk about.
If you place a part in the virtual workspace of WinPC NC, it will not start the job if there are parts of the drawings out of these boundaries.
SC 420 mit DIY parallel + Proxxon mit Mod + HF500 + SprintLayout + LibreCAD/QCAD + FreeCAD +WinPC starter/USB->EstlCAM + EstlCAM LPTAdapter + EstlCAM Handrad + DIY Vakuumtisch
Gruß, Andreas
Well, you're right. Moving just one axis a time and waiting for the switch can be used to set a reference point.
Do you want to laugh? With linuxCNC when the router triggers one switch the program stops. I have to:- turn off steppie power
- manually move the router a little back (so the switche is no more triggered)
- turn power againFunny! 🙂
Anyway happy to know that it's not easy to damage motors when the end-position is physically reached.
Axis switches are for nothing? This can be... so why not eliminating them at all?
Yes, 3 are useful to have a reference position... but 6 switches would be better! A simple program could calculate the working area quite easily as a 3D volume using just 2 points in the 3D space.Anyway, what above are just my speculations...
There seems to be something wrong with your LinuxCNC config then. Normally the switches should not be triggered when running a program on the machine.
Please refer to this Thread for screenshots on the setup of the axis. Note the position of the switch as a negative value on the x-axis. On the y and z-axis note the difference in the values of "Table Travel" and "Home (Switch) Location"!
Cheers,
Christian
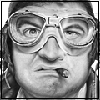
Please refer to this Thread for screenshots on the setup of the axis. Note the position of the switch as a negative value on the x-axis. On the y and z-axis note the difference in the values of "Table Travel" and "Home (Switch) Location"!
Cheers,
Christian
Danke Christian, I will check that thread!
(na ja... ich sollte Deutsch lernen :dry: )
SC300 + Spindle HF500 + Portalerhöhung + LinuxCNC + gsimple
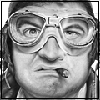
Thanks to MagIO2 and Chris. 🙂
I was wrong, the switches of the Stepcraft are just used for reference purposes (i.e. to allow the software to fix a well-know position of the router relative to the working area).
They are not "limiting" switches (i.e. to avoid the router runs out of the maximum allowed travel distance). So I had set wrongly the pin #12 of the parallel port by using the "All limits" value, while the correct choice was "Home" instead.
Unfortunately, even on linuxcnc.org, there is a lot of technical "jargon" that doesn't helps newbies like me... 🙁
Soon I will post my working configuration on this forum. Tschuss!
SC300 + Spindle HF500 + Portalerhöhung + LinuxCNC + gsimple
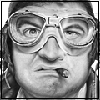
My correct configuration for home switches is here.
SC300 + Spindle HF500 + Portalerhöhung + LinuxCNC + gsimple

Those switches are not for stopping a machine which runs crazy.
And even then. I once saw an MDF boards stack carrier and distribution robot, 4m+ tall, take a life of his own, go past electro-optical and mechanical limit switches, carry on like a herd of cows thanks to Newton's First Law, go past the building gate that luckily or unluckily was open then off to the road, finally ending up on a stream.
It was spectacular. No-one was hurt except the vendor's pocket 😆
Clockwork Orange is a S600 with 4th axis, Kress 1050. Software is UCCNC, DeskProto, Rhino, DraftSight. Also a Silhouette Cameo for vinyl, plastic card, etc.
- 44 Foren
- 7,336 Themen
- 63.2 K Beiträge
- 15 Online
- 26.3 K Mitglieder