Moin,
Das war , wie geschriieben, ein Reststück und gab gerade die 25mm her; ...
Ok, ok, ich hab nur nachgefragt, weil es ja auch noch andere Anwendungsmöglichkeiten geben könnte.
Außerdem hast du mich gerade auf eine andere Konstruktionsidee gebracht.
Ich zeig die, sobald ich die ersten Pratzen davon gefräst hab. Muss nämlich noch die Größen richtig bestimmen.
sswjs, aka Jens
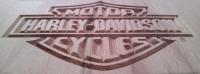
Hallo Michael,
was für einen Fräser hast du da benutzt?
Wilhelm

Moin Wilhelm,
hier ist der Link:
Gruss
Gruss Michael
begonnen mit 420/2, Alu-Fräse "KARLA" (noch im Bau)
EstlCam mit Arduino NANO, WinPC-NC USB
Kress, QCAD, Fusion 360, Inventor, Winghelper
Moin,
so, ich hab jetzt mal Angabenüberprüfung gemacht. Hier meine Ergebnisse:
Fräser: VHM 2mm Fisch
Bis 3mm Tiefe
ohne Kühlung, 5mm/sek und 1mm Zustellung geht.
Ab 3mm Tiefe
ist ein KSS (Kühl - Schmier - Stoff) erforderlich, denn an den Rändern reibt sich der Fräser auf und frisst Material. Dabei, mit 5mm/sek und 1mm Zustellung, bricht die Proxxon massiv ein.
Ab 4mm Tiefe
Auch mit KSS war ein Zurücknehmen des Vorschubs auf 4mm/sek notwendig. Eine Veringerung der Zustellung bei Beibehaltung des Vorschubs brachte das selbe Ergebnis, Proxxon brach ein und Fräser frisst Material in der Seite.
6mm/sek hab ich auch probiert, in 4mm Tiefe und mit 1mm Zustellung brach der Fräser...
... was die Angaben zur Spandicke in den Tabellen von Sorotec betätigt.
Fazit: 4mm/sek und 1mm Zustellung sind bei Säuberung des Fräskanals bis 8mm Tiefe, mehr hab ich noch nicht probieren können, problemlos möglich.
Material: AlMg4,5Mn 8mm dick
sswjs, aka Jens

Moin,
ich bin es leid - die serienmässigen Spannbrücken von Stepcraft sind ständig im Weg, irgendwo steht immer eine Spannschraube zu hoch, der Stopschalter wird schon schwindlig ...
Also musste eine neue Spannplatte her, da meine Alu-Nuten-Platte ziemlich verzogen ist und (bei mir) die Nuten auch nicht exakt parallel laufen (bohr ich an einem Ende eines Werkstücks 2 Löcher im Nutenabstand, stecke zwei Sechskant-6mm-Schrauben in die entsprechenden Nuten, die Schrauben dann durch die vorher gebohrten Löcher und versuche, das Werkstück dann mit diesen Schrauben bis ans Ende des Arbeitsbereiches zu schieben, geht´s bis zur Hälfte und dann ist Schluss, dann laufen die Sechskantköpfe an den Nutenwangen fest).
Nein, sie verkanten sich nicht, entsprechende Markierungen habe ich angebracht ...
So bot sich als Spannplatte eine 22mm-MDF-Platte an (von OBI, Bezeichnung: MDF roh E-1). Plan-Abweichungen über die gesamte Platte VOR Bearbeitung <0,03mm. Das ist mehr als OK.
In die Platte sollten im 50mm-Raster Gewinde-Einsätze eingedreht werden, folgende Teile brauchte ich dazu:
- Platte 300x400mm, darauf passen
- 48 Gewinde-Einsätze M4 (8x10) und recht teuer (0,50€/St.), dazu benötigte ich
- einen Bohrer 6,5mm für die Kernlöcher
Da ich keinerlei Vorrichtung habe, um eine so grosse Platte exakt einzuspannen UND die Löcher millimetergenau zu bohren (ich habe nur den Proxxon-Kreuztisch, der mir hier nicht weiterhalf), habe ich mit der Steppi die Kernlöcher exakt in den Dimensionen 1mm tief "vorgebohrt" ...
... dann mit der Proxxon (dafür kann man sie auch benutzen!) Zentrierbohrungen 1mm angebracht und danach "freihändig" am Bohrständer die Kernlöcher gefühlvoll weitergebohrt, "möglichst" genau ("möglichst" deshalb, weil erstens die Zentrierbohrungen nicht 100% exakt waren und ich zweitens die Bohrerspitze irgendwie genau in die Zentrierbohrungen kriegen musste). Bis auf 2 Ausrutscher auch hinreichend genau geworden.
Zum Schluss - die zeitaufwendigste Arbeit - die 48 Gewindeeinsätze eingedreht. Zufällig hatte mir der Verkäufer (weil er es wohl nicht besser wusste) zwei Sorten Einsätze in die Tüte gepackt: welche mit Schlitz für Schraubendreher und welche mit Innensechskant für Inbusschlüssel.
Die mit Schlitz liessen sich eindeutig schlechter ansetze und senkrecht eindrehen, da musste ich sehr oft neu ansetzen und gefüüüüüühlvoll drehen, um sie halbwegs lotrecht reinzubekommen (was nicht immer gelang);
die für Inbus liessen sich besser ansetzen und durch die Hebelwirkung des Inbusschlüssels auch leichter korrigieren, sodass diese Einsätze insgesamt wesentlich besser und genauer einzudrehen waren.
Leider verhielt sich die MDF-Platte genau so, wie ich es erwartet/befürchtet hatte, nämlich wie eine normale Spanplatte: die Lochränder brachen teilweise schichtförmig ab und um die Einschraublöcher ergab sich ein ringförmiger Wulst (durch das vom Einschrauben verdrängte Material), sodass die Platte am Ende aussah, als hätte sie 48 kräftige Pickel. So war die Platte nicht zu gebrauchen, der Bandschleifer musste her und die "Pickel" wurden abgeschliffen.
Dass die Platte danach nicht mehr plan war, war eigentlich sonnenklar, umso überraschter war ich, nachdem ich sie in alle Richtungen mit der Messuhr abgefahren hatte: die Abweichungen waren nirgends grösser als 0,07mm. Immer noch gut - aber morgen werde ich sie mit 0,1mm planschleifen ..
Ob sich die Arbeit gelohnt hat, immerhin ttl. 6 Stunden, weiss ich noch nicht; ob die Spannplatte praktikabel ist und meine Erwartungen erfüllt, wird sich herausstellen ...
Gruss
Gruss Michael
begonnen mit 420/2, Alu-Fräse "KARLA" (noch im Bau)
EstlCam mit Arduino NANO, WinPC-NC USB
Kress, QCAD, Fusion 360, Inventor, Winghelper
..
Die mit Schlitz liessen sich eindeutig schlechter ansetze und senkrecht eindrehen, da musste ich sehr oft neu ansetzen und gefüüüüüühlvoll drehen, um sie halbwegs lotrecht reinzubekommen (was nicht immer gelang)
...
das geht aus meiner sicht folgendermaßen besser: gewindestift in gewindebuchse drehen, 2 muttern drauf bis anschlag. die zweite ist zum kontern. nun das ganze sanft in nem bohrständer mit eingespannter bohrmaschine einspannen.
1. die bohrmaschine läuft nicht, das ganze dient nur zum senkrecht halten!
2. mit sanft ist gemeint, dass der gewindestift nur im futter zentriert und nicht gespannt wird.
das ganze unter leichtem abwärtsdrücken des bohrständers mit nem schraubenschlüssel eindrehen.
das hat natürlich nen haken, wenn die grundplatte des ständers nicht drehbar ist^^. dann ist man auf werstückegrößen kleiner der ausladung des bohrständers begrenzt. falls der ständer drehbar ist ganz einfach diesen auf das werkstück stellen bei der aktion. so hab ich auch m8 in multiplexplatten gedreht.
bei dem "ausbruchproblem" hilft folgendes: größer vorbohren, reduziert auch die kraft, die beim eindrehen der buchsen auf tritt. zur not dann einkleben. bei m4 ist die kraft vielleicht noch egal, bei den größeren irgendwann dann nichtmehr.
Andreas

Moin,
Klar, das isses - der Tip (samt Anleitung) ist so gut, dass ich das morgen versuchsweise ausprobieren werde an einem kleinen Brettchen!!!
Leider habe ich keinen Bohrständer mit drehbarer Grundplatte; werde es so machen, wie ich es bei meiner Platte gemacht habe: Kreuztisch auf Grundplatte Bohrständer, Werkstück mit "normalen" Spannpratzen befestigen und Kreuztisch mit den Support-Kurbeln von Bohrloch zu Bohrloch kurbeln. Geht.
"Ausbruchproblem": habe selbst überlegt, grösser vorzubohren; da ich aber befürchtete, dass die Gewindeeinsätze dann nicht mehr halten, hab´ich es gelassen. einkleben wollte ich noch nicht, da ich vielleicht noch mehrmals planen will/muss und ich dann die Sacklöcher ev. vertiefen muss, damit die Einsätze nicht überstehen ...
Also noch ´mal: DANKE!
Gruss
Gruss Michael
begonnen mit 420/2, Alu-Fräse "KARLA" (noch im Bau)
EstlCam mit Arduino NANO, WinPC-NC USB
Kress, QCAD, Fusion 360, Inventor, Winghelper

Hallo Michael,
was für einen Fräser hast du da benutzt?
Wilhelm
Moin Wilhelm,
habe heute nachmittag Alu 8mm (für Spannpratzen) von der Platte gefräst und dafür den Fräser von STEPCRAFT genommen.
Geht ebenfalls. Hier ein paar Daten zum Vergleich:
Sorotec (Art.N. L2SA.0200)
- Nutzlänge ca. 7 mm
- sehr lange Standzeit des Fräsers
- Preis 5,60
Stepcraft (Art.Nr. 10097)
- Nutzlänge ca. 12 mm !!!
- Standzeit kann ich noch nicht beurteilen
- Preis günstiger - 3,70
So sieht die Fräskante mit dem Stepcraft-Fräser aus:
Gruss
Gruss Michael
begonnen mit 420/2, Alu-Fräse "KARLA" (noch im Bau)
EstlCam mit Arduino NANO, WinPC-NC USB
Kress, QCAD, Fusion 360, Inventor, Winghelper

Moin,
dieser post ist sozusagen nahtlose Ergänzung zum vorigen: die Stepcraft-Fräser sind alle (!) im Fräserhimmel. Mangelnde Standzeit oder Festigkeit kann ich zum jetzigen Zeitpunkt nicht behaupten, will es aber auch noch nicht ausschliessen.
Der Reihe nach:
Nachdem ich vorgestern ein entsprechendes Stück Alu 8mm sauber mit einem Stepcraft-Fräser Nr. 10097 von einer grösseren Restplatte abgetrennt hatte, ging es gestern ans Fräsen von 2 Spannpratzen (das Tutorial von "Andreas" [MaglO2] - s. Foto 1) lag ausgedruckt und griffbereit auf der Werkbank), das Werkstück eingespannt auf meiner Arbeitsplatte. (Foto 2)
Als Vorbild dienten mir die von "Jens" [sswjs] konstruierten Spannpratzen , die ich für meine Anforderungen etwas modifizierte (die 5mm tiefe Ausfräsung des Langlochs für die Köüfe der Inbusschrauben habe ich mir gespart, ich will M4-Schrauben benutzen),; begonnen wurde mit der überstehenden Nase der Pratzenspitze. Fräser: der schon vorgestern benutzte Stepcraft-Fräser;
- Zustellung 0,5 mm
- Vorschub 6 mm
- 20.000 U/min
(Foto 3)
Es folgten die Langlöcher mit demselben Fräser und den gleichen Parametern. Das erste Langloch wurde problemlos bis auf die gewünschte Tiefe von 7,8 mm gefräst.
Beim zweiten Langloch lief es problemlos bis zu einer Tiefe von 6,5 mm durch, dann brach die Proxxon langsam ein, erholte sich und brach dann in der rechten Rundung des oberen Langlochs massiv ein - und knacks. gestopt, Fräser gewechselt, neu z-genullt: an der gleichen Stelle: Einbruch Proxxon - und knacks. Nanu!?
Nächsten Fräser eingespannt, neu z-genullt, Vorschub verringert - in besagter Rundung wieder: knacks!
Fräser gewechselt ... und mit KSS (Spiritus-Wasser-Gemisch) gekühlt - Knacks, Fräser Nr. 3 perdu
Jetzt wollte ich es wissen
Fräser gewechselt (Nr. 4) ... mit Bohröl gekühlt - na ihr wisst schon
Fräser gewechselt (Nr. 5, der letzte) - immer an der gleichen Stelle !!!
(Foto 4)
WARUM ???
- liegt´s am Fräser? (Aber das erste Langloch wurde dochg anstandslos gefräst ???)
- liegt´s am Material (es ist ein Restposten und deutlich als Randstück zu erkennen)
- wird das Werkstück durch die Spannung "gestaucht"?
- vibriert die Stepcraft (der Fräser brach immer an der gleichen Stelle am Hals und steckte im Werkstück fest)
- hat sich irgendwas an der Stepcraft gelockert oder verstellt?
Auf alle Fälle werde ich heute nachmittag die Stepcraft genau untersuchen.
Ich hoffe auf Antworten/konstruktive Kritik.
GRuss
PS. Habe bei Sorotec lange Alu-Fräser (nutzbare Schneidlänge 12mm bestellt - sehr teuer)
Gruss Michael
begonnen mit 420/2, Alu-Fräse "KARLA" (noch im Bau)
EstlCam mit Arduino NANO, WinPC-NC USB
Kress, QCAD, Fusion 360, Inventor, Winghelper
Moin,
es ist...
...dein Vorschub.
Bei 6mm/sek brachen bei mir auch alle Fräser :S
4mm/sek ist zwar noch machbar aber hart an der Grenze. Ich fräs aktuell wieder mit 3mm/sek und 1mm Zustellung mit der Proxxon.
sswjs, aka Jens
PS: ich kann dir gerne ein paar Pratzen fräsen, aber 7,50 müsste ich auch pro Pratze aufrufen...

Sehe ich das richtig und das Werkstück ist nicht von oben festgespannt? Wenn das so ist, dann könnte ich mir vorstellen, dass die Fräser abbrechen, weil sie das Material nach oben ziehen und dann in der Fräsbahn verkanten.
Wahrscheinlicher noch kommt es daher, dass der Kern der Langlöcher ja völlig unfixiert ist.
Ich hab ja jetzt schon so einiges in Alu gemacht, aber sowas ist mir noch nicht passiert. Ich glaube ich hab noch keinen einzigen Fräser beim Alu fräsen verloren - nur beim versehentlichen dagegen fahren ;o)
Nur in Messing hatte ich vermutlich mal ein ähnliches Problem. Es gab da eine Ecke, die abgefräst werden musste und diese Ecke hing in der Luft - war zu klein zum festspannen. Als nur noch wenige mm zu fräsen waren fing - so vermute ich - diese Ecke an zu schwingen und hat auch den Fräser verkantet.
Also mein Tipp: beim Fräsen von Metallen muss wirklich alles bombenfest sitzen, auch sowas wie die Kerne der Langlöcher. Wenn es sich nicht direkt fixieren lässt, dann muss man mit Stegen arbeiten, oder es ggf. als Tasche komplett ausfräsen, was dann aber wieder die Standzeit des Fräsers unnötig verringert.
Und ja, der Vorschub scheint mir auch ein wenig sportlich.
SC 420 mit DIY parallel + Proxxon mit Mod + HF500 + SprintLayout + LibreCAD/QCAD + FreeCAD +WinPC starter/USB->EstlCAM + EstlCAM LPTAdapter + EstlCAM Handrad + DIY Vakuumtisch
Gruß, Andreas
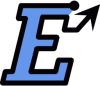
Hallo,
...dann brach die Proxxon langsam ein, erholte sich und brach dann in der rechten Rundung des oberen Langlochs massiv ein - und knacks. gestopt, Fräser gewechselt, neu z-genullt: an der gleichen Stelle: Einbruch Proxxon - und knacks. Nanu!?
bei einbrechender Drehzahl würde ich 2 Ursachen in die nähere Auswahl bringen:
- Aufbauschneiden (Alu pappt am Fräser an) - z.B. weil die Späne aus der engen, tiefen Nut kaum noch rauskommen -> dagegen spricht jedoch, dass es immer an derselben Stelle passiert...
- Oder das Restmaterial im Inneren ist verspannt und klemmt den Fräser kurz vorm Durchstich ein wie MagIO2 schon vermutet hat...
Ob Aufbauschneiden Schuld sind kannst du am abgebrochenen Fräserende sehen - wenn das "blank" ist war alles OK, ist das mit Alu vollgeschmiert hat der Faktor zumindest eine Teilschuld.
Gegen beides helfen 3 Tricks:
- Den Ausschnitt komplett räumen lassen, so dass nichts stehen bleibt das den Fräser einklemmen kann. Dauert zwar länger, ist für den Fräser aber erheblich sicherer...
- Entlastung fräsen: Wenn du zuerst eine etwas nach innen versetzte Fräsbahn z.B. bis 2/3 Tiefe fräst
und dann erst die eigentliche auf voller Tiefe schaffst du Luft in der Nut. In dem Fall jedoch uninteressant, da innen nicht viel Material steht und du da auch gleich alles komplett wegfräsen kannst wie oben vorgeschlagen... - Das Teil innen an ein paar dünnen Stegen hängen lassen die nach dem Fräsen manuell entfernt werden. Das ist schnell und verhindert Klemmer, ändert aber nichts daran, dass die Späne es schwer haben an die Oberfläche zu kommen...
Viele Grüße
Christian

der Vorschub scheint mir auch ein wenig sportlich.
Das habe ich auch als Möglichkeit in Betracht gezogen.
Aber warum sind der gerade Schnitt und das erste Langloch einwandfrei durchgegangen? Und bei Alu 3mm bzw. 5mm ging´s durch "wie Butter"?
Egal: Vorschub wird drastisch gedrosselt, zunächst auf 3mm - dann halt weniger sportlich ...
da kannst Du rechthaben mit der unzulänglichen "Spannerei"; aber: das gilt nur für Fräser 1+2, danach hab´cih selber daran gedacht, zusätzlich noch von oben zu spannen (s. Foto). Trotzdem hat das bei Fräser 3 bis 5 nichts gebracht ...
Wahrscheinlicher noch kommt es daher, dass der Kern der Langlöcher ja völlig unfixiert ist.
Das leuchtet mir ein: bei 6,5 bzw. 7mm erreichter Tiefe kann der verbliebene Teil des Kernlochs tatsächlich vibrieren, lässt sich ja locker mit einem Finger bewegn. Und bei den Kräften, die selbst in so einer kleinen Fräse auftreten ... Also scheint mir die Fixierung mit Stegen tatsächlich die erste Wahl - oder?
Deinen Beitrag (super erklärt!) hab´ich erst später gesehen, er deckt sich zum grossen Teil mit dem von Andreas, Strategie ist klar: wenn die nachbestellten Fräser - diesmal wieder von Sorotec, extra lange Spezialfräser (etwa so lang wie die von Stepcraft) - da sind, werde ich ...
... ein Langloch als Tasche fräsen
... ein Langloch mit Stegen
jeweils Zustellung 1mm und Vorschub 3mm
Aber danke für Eure Kommentare, sind hilfreich!
Gruss
Gruss Michael
begonnen mit 420/2, Alu-Fräse "KARLA" (noch im Bau)
EstlCam mit Arduino NANO, WinPC-NC USB
Kress, QCAD, Fusion 360, Inventor, Winghelper
Moin,
um dir mal die Illusionen zu nehmen, dein Fräser wäre glatt durchgegangen:
Die roten Pfeile zeigen auf die Stellen, wo dein Fräser angefangen hat Material zu fressen.
Zwei mögliche Ursachen kann ich auch benennen:
1. Keine Kühlung bzw. Schmierung
2. Fräskanal voll Späne
Ich hab nicht umsonst eine Spritzflasche mit wasserlöslichen Schmiermittel. Ich spritz damit nämlich auch den Fräskanal frei...
sswjs, aka Jens

Moin Jens,
da bin ich nun echt erschrocken - und ziemlich desillusioniert ! Trotzdem: Danke.
Gruss
Gruss Michael
begonnen mit 420/2, Alu-Fräse "KARLA" (noch im Bau)
EstlCam mit Arduino NANO, WinPC-NC USB
Kress, QCAD, Fusion 360, Inventor, Winghelper
- 44 Foren
- 7,424 Themen
- 63.4 K Beiträge
- 1 Online
- 26.5 K Mitglieder