STEPCRAFT HF spindle
The STEPCRAFT HF spindle is a great addition to your STEPCRAFT system. Bigger cutters and much quieter. It really does open up a lot more possibilities!! Ready to go out of the box.
https://www.youtube.com/watch?v=oSvpZiPZf7Q

Hi,
the nut for the HF spindle...there's a collar inside the nut, why is it non-concentric? It makes all bigger tools wobble because of the nut that is not centering it..
I ordered new nut(s) and they are the same...can't really do nothing with the SC600 now :angry:
br
Markku
www.stepcraft.fi (reseller in Finland)
www.sloworks.fi
SOLIDWORKS, WinPC-NC Full, EstlCAM, SC1/600 + HF500W, laser
BCN3D Sigma
hi markku,
i think u make the same mistake than me in the beginning:
the ER11 collet must snap in then there is wobbeling nothing any more. but if you use the diameter 8 mm you will need at least two clamping nuts because it is really difficult to get it out again.
with the smaller diameters there is no problem.
Andreas
you must "snap" the collet into the nut before you tighten. if you do not mount your tools correctly its lethal. the collet should "seat" / "snap" into the nut flush with the locking surface. You must also be careful with cutter sizes in the collet. For example - its not a good idea to put a 1/8th inch cutter into a 3mm collet. If the cutter is "slightly" larger than the collet - the collet will spread and loose concentric alignment when you tighten.
its also not a good idea to use an undersized cutter in a collet thats not designed for it. ER20 collets (in sizes above 4mm) can work with up to 1mm undersized cutters (5.2mm will work in a 6mm collet for example). ER11 collets do not have the same tolerance.
if you have a 1/4 inch shank cutter - use a 1/4 inch collet. if its 1/8th use 1/8th. if its 6mm use 6mm etc etc..
the radial force on the spindle system (the force on the system in the XY plane) due to the rotation of the spindle - is related to the ^2 of the angular velocity (RPM) and the eccentric load/mass (how well/badly balanced the spindle is). If you increase the RPM by a factor of 2 you increase this force by a factor of 4. this is important as its very important your tools are mounted correctly into the spindle. This is also why you see the two holes drilled. This is to balance the nut.
"wobble" will exert much higher radial forces than normal and will shorten the life of the spindle bearings. its also dangerous - be careful here and figure out whats causing this.
The "eccentric" feature that you see is part of the ER collet design. it called an "eccentric extractor ring" - its designed to carry out 2 functions.
1 - its designed to keep the collet and the nut "together" as a unit when handled
2 - as the nut is loosened - this eccentric rings extracts the collet from the spindle bore - this is why the collet does not get stuck in the spindle bore when you loosen the collet nut.

Hi,
and thanks! I have totally missed that "snap collet first to the nut"...my mistake :whistle:
Succesfully machined one bambo piece 🙂
br
Markku
www.stepcraft.fi (reseller in Finland)
www.sloworks.fi
SOLIDWORKS, WinPC-NC Full, EstlCAM, SC1/600 + HF500W, laser
BCN3D Sigma
Super!
I've got the HF Spindle running on a Mk1 420.
The question I've got is how to control the speed from within UCCNC? I've got the parallel cable connected between the CNC control board and the box for the spindle gubbins. Is there some configuration to be done within UCCNC?
Also I'm looking at hooking up an electrical tool height switch by connecting one wire to the metal work piece and the other to the spindle body. Has anyone tried this already? Any hints and tips?
Many thanks in advance.
Rob
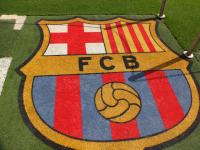
Hi Rob,
regarding your 2. question I placed a post in the German section of the forum:
So it's in German 🙂
Short Translation:
I bought the sensor at ebay and connected one wire with the metal body of the sensor. This wire is connected on the plug side with pin 8 of X2. Therefore the sensor body should be insulated from ground. The other wire of the sensor is connected to ground (pin2 of X2) as well as the spindle and the tool.
In that case the UCCNC will notify an electrical contact when the tool touches the surface of the sensor. In addition if there is no electrical contact the sensor-switch will give the contact finally. But in that case this function is only for security reason since you need to add the offset value in the macro M31 measured from the sensor surface.
You will find a Video and a link to the M31 macro in the post.
Don't Forget to configure the sensor in UCCNC.
Hope that helps!
Regards
Hartmut
Viele Grüße
Hartmut
V2/420 China 800W wassergekühlt
UCCNC & ARDUINO ESTLCAM Controller
ESTLCAM & QCAD
-----------------------------------
DK5LH/G11
Hey Doc,
That's not really what I was after as that will only tell you the height at the sensor. Instead of making the electrical contact within the switch, I'm planning on connecting a wire to the aluminium that I'll be milling, and connecting the other wire to the spindle, then when the endmill touches anywhere on the work piece, it will close the connection.
This is also a great way of milling PCBs as you can probe the height anywhere on the work.
Not sure if that makes sense?
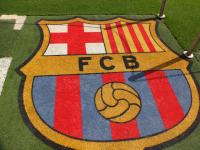
But thats the same!
The tool just touches the sensor switch surface which is connected to the sensor input on X2. Instead of my sensor you can use any metal part like your work piece. Your tool must be grounded of course. And...your work piece must be insulated from the machine table. In my case I've to add a static offset value (sensor height) to the M31 macro. If you don't have any sensor height because the tool contacts the work piece surface this offset value has to be set to "0" in the macro.
I'm just using my original sensor because in case of there's no electrical contact the switch is working as a mechanical buffer which gives hopefully contact one millimeter later and stops the Z axle movement. Hope it's clear now.
Viele Grüße
Hartmut
V2/420 China 800W wassergekühlt
UCCNC & ARDUINO ESTLCAM Controller
ESTLCAM & QCAD
-----------------------------------
DK5LH/G11
I think I'm with you now. So the endmill will be connected to to ground? I did I quick test and the body of the spindle isn't connected to the collet, but haven't tried the ground terminal yet.
The question about controlling the spindle through UCCNC is still bugging me though.
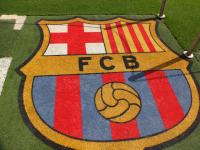
You are right! And yes, if the endmill has no contact to ground it will not work. I'm using a China spindle which gives contact to the endmill and the machine ground. Also the machine ground has contact to the logical / digital ground of the control unit. This is important since you need a complete electronic "circle".
The tool sensor input on Pin 8 of X2 is logically high (5V) if ther's no contact. It drops to 0V if you connect it to ground. And that stops the Z-axis movement immediately...if your M31 Macro is working 🙂
Viele Grüße
Hartmut
V2/420 China 800W wassergekühlt
UCCNC & ARDUINO ESTLCAM Controller
ESTLCAM & QCAD
-----------------------------------
DK5LH/G11
To get spindle controlled by UCCNC you need to make sure your configuration for that it is correct. I.e. go to the confugration / Axis setup / Spindle page, and make sure PWM spindle is set, and PWM pin is set to 17, and port 1. PWM freq should something like 900, and min and max duty 12 and 100. Also set the min spindle velocity to 3000 and max to 20000. Those settings will allow you to configure the speed on the UCCNC.
To turn it on and off, make sure Spindle relay output is enabled, and M3 relay pin is 1, and port 1. You might want to set the M3 delay after start to be 3000 or 5000, just in case spindle does not start, so you have time to stop it before it starts doing cuts. I have had some issues that spindle does not always start when UCCNC instructs it to do so.
You can look examples for configuration and issues with HF spindle starting from the thread.
Stepcraft 2 840 Kickstarter make anything package
HF500, 3D print, Drag Knife, etc
UCCNC + UC100, V-Carve
Thanks for the info Kivinen, however it's not working just yet.
Interestingly, when I set both the PWM Pin and the M3 Spindle Relay Pin to Active High, the spindle switches on to max rpm, so there is some life in it, but just not what I'm after.
Here's my settings for reference. I've also looked through the linked thread but not luck.
- 44 Foren
- 7,436 Themen
- 63.4 K Beiträge
- 3 Online
- 26.5 K Mitglieder