UCCNC autoleveler plugin
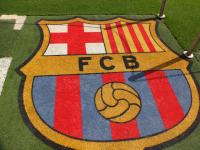
Found in an other forum a "autoleveler" plugin. Didn't install it at the moment, but I think it's great for engraving, especially for PCB milling. Currently I use for this operation ESTLCAm with the Arduino board but now it seems also to be possible with UCCNC:
There are also 3 videos available:
You need to be member of the forum and have to register before download the zip-file. Check the complete post for the latest version 1.0019 of the plugin
Viele Grüße
Hartmut
V2/420 China 800W wassergekühlt
UCCNC & ARDUINO ESTLCAM Controller
ESTLCAM & QCAD
-----------------------------------
DK5LH/G11
Hello.
Can anybody add the autoleveler plugin in this thread?
I have been trying to activate the account on cnczone.com the last month without any success.
I use icloud.com email, and i sadly never get any activation email.
/Terje.
The Autoleveler plugin still comes with UCCNC, You just have to activate it....
Produktevangelist 🙂
Es grüßt mit der Ihm gegebenen Freundlichkeit...
...der Thomas
Thank you ThomasDbg.
I didnt realize that there where a new version out.
Maybe i'll finaly can get it running.
The leveler version i found earlier would only crash and say overflow memory, or so..
BR
Terje.
I just purchased the Stepcraft Probe and installed it. Have not used it yet however.
If you want to use their level of implementation of the autoleveler, check out the downloads tab for links
https://stepcraft.us/product/touchprobe/
Functionally, it is working.
Stepcraft 2 420
500 Watt Spindle
3D Printing System
3d Probe
T-Slot Table
Tooling:
1/8" 60 Deg 4 Flute V Bit
1/8" 4-Flute Square Nose End Mill
1/8" 2 Flute Ball Nose End Mill
1/16" 2 Flute Ball Nose End Mill
UCCNC and VCarve Pro
Total Newbie!
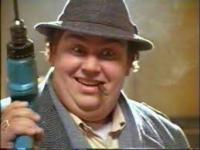
Hi we have a stepcraft 840 here and use the autoleveller all the time for milling pcbs. we are using the latest version of uccnc with the autoleveller .dll plugin activated.
we have got the tool length sensor here and i cut the cable half way along after milling a custom pcb that allowed that and two independet wires to be attatched to the blank pcb and the milling bit.
when the uccnc software starts the plugin runs and i load in the gcode file and set the probe spacing etc.
my steps are.
1: load file into uccnc
2: home the 840
3: move to my datum point on the workpiece (blank copper board)
4: attach the cables to the board and milling bit
5: probe zero
6: goto the plugin window for autoleveller and click send to stepcraft
7: run probe cycle with out the spindle being powered!!!! ( when you click send to stepcrfat it edits the gcode and adds the probe points to the file)
8: once probing has finished remove probe wires
9: run cycle with spindle running.
10: wait for milling to finish.
I will add a few pictures this weekend.
8:
Hi,
I've done all the Steps as you explained it in your last comment.
I had no problems running the probe cycle and starting with the milling.
But he did not use the values, that he had measured before.
The Mill is always using the predefined values of the gcode but not the adjusted values from the measurement.
Could anyone help me with this problem?
I had great results using the Plugin in combination with microstepping (text in german, but there are photos at the end):
https://www.stepcraft-systems.com/en/forum/fraesen/4900-microstepping-mod-isolationsfraesen#50995
This lets the autoleveler work with height-differences of 0.0009375mm instead of the normal 0.0075mm and greatly improves overall precision, especially important for fine pitch milling like 0.4mm.
@IrrgangD Maybe you should update to the latest Version v1.0045
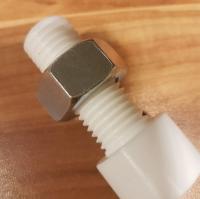
I have a question regarding the initial zeroing before probing the surface:
1. At which position do i need to manually zero the z-axis before running the probing session?
2. How does to "auto zero" function in the plugin work and what's the meaning from the XP and YP fields?
Thanks for your help.
CNC: Stepcraft 2/840, Kress 800-Q FME, Estlcam, Deskproto 7 Multi-Axis, Umgestiegen von WinPC NC USB v3 auf UCCNC 1.2049
3D Printer: Prusa MK3S mit MMU2S, Creality CR-10, Anycubic Photon
I expected, that the probe must be zeroed on the surface before it autoprobes the workpiece. Is it relevant where this z0 is defined? Can it be just any point on the workpiece as long as its x0 and y0 are known?
Concerning your question:
1. At which position do i need to manually zero the z-axis before running the probing session?
I expected that z0 should be set either
a) where z0 was defined before with the probe (on the same x- and y-position) or
b) on the last point of auto-probing, since the gcode prompts to "now manually find z0" or so.
Anyway, it didn't work so far for me, so i'm grateful for any hints.
- 44 Foren
- 7,436 Themen
- 63.4 K Beiträge
- 3 Online
- 26.5 K Mitglieder