Dear user, the forum software has been updated. For the first login please reset your password.
Basic Mach3 configuration data
Since there are several people who use Mach3 as their control software it would be very helpful to have some sort of basic and safe configuration data available. For example the pin assignment chart states that reference switch X/Y/Z is pin 12 and I can see in the machine parameters page that reference switch at the end (X-axis) is negative, reference switch at the end (Y-axis) is positive, reference switch at the end (Z-axis) is negative and order reference drive is z-x-y. What does all that mean? For the X axis in Mach3 I can assign pins for X++, X-- and X home, what should I choose? Another example is the motor acceleration and speed values. Stepcraft systems are available as ready-to-go machines that must have some sort of basic settings preprogrammed. Why not translate those settings into Mach3 language. It doesn`t have to be a ready made configuration file, numerical data would be good enough. Advanced users could experiment with the settings and get the maximum out of their machine, but for an average user it would save a lot of time.
Stepcraft 600SF (version 1) parallel port
Proxxon IBS/E
Mach3
devCad Cam Pro; devWing Cam; devFus Cam; Profili Pro 2
All limits pop same pin on SC - its the way its wired. The reason there is X++ and X-- and X home - is that on some machines - there are three individual switches for each of these functions.
You should choose the X home switch for pin 12 - if you would like to home the machine.
Then assign X++ or X-- to 12 also. Either or.. Whenever the machine is not in the "homing function" it will stop when you hit the switches and "trigger the limit switch".
On bigger machines - for example with heavy duty servo - the machine cannot crash on either side of the gantry. As this would be catastrophic. For SC its no biggie as the stepper motor simply torques out and buzzes... not good to go it all the time - but it does not damage the machine in the same way a bigger machine would.
Mach won't home unless there is a switch assigned to home pin.when homing ignores limits and only looks at home pins. Then once homes limits are active.
Mach3 motor tuning has the options to change both the accelerations and the speed. The speed is the Max speed of the axis. Which you will get when you jog at 100%. If you input a feed in your program that is greater than your Mach3 feed - you will simply get the max speed. SC max speed is 1800mm/min. We have had machines running at 2,500mm/min - but have to be perfectly tuned. Drive voltage is 19V DC. drives can take 30V DC is seems (not sure if this is stable) increasing stepper voltage will increase torque. So in theory if one was to run the SC on 30V DC you could get a lot more power and speed.
NOTE: The speed assumes the "Steps per" is correct. That is steps per unit - is such that the output from the machine (how far / fast is physically moves) is correct. For SC its 200 steps / unit (mm). So once this is correct then the feeds and accels are correct.
Acceleration is down to the drive system. If you ask the machine to to from 0 - max speed at too high an acceleration it simply cannot manage it. This is a physical limitation.
Attached is a working profile (at least it was last time I checked). We used the data from SC and some of our experience. its by no means the "best"...
If you use / change / tweak ... post what you find.
The best way to learn is to do.
Feel free to ask q's
Thanks for another informative post.
If we look at:
5030.200.200.30.200.200.16.67250.200.
Does this mean that X axis steps per unit is 200, speed is 1800 mm per min and acceleration is 200mm/sec/sec; Y axis steps per unit is 200, speed is 1800 mm per min and acceleration is 200mm/sec/sec; Z axis steps per unit is 200, speed is 1000.2 mm per min and acceleration is 250mm/sec/sec?
When I was trying to figure things out on my own based on the manuals and pure random chance I arrived at the numbers 200mm per unit for all axes, 1800mm/min for Y and X, 1500mm/min for Z, acceleration for all axes 480mm/sec/sec, step pulse 1 and dir pulse 0.
I`m not looking for the most optimum setting at this point. I just want my machine to work similar to the promotional videos.
Stepcraft 600SF (version 1) parallel port
Proxxon IBS/E
Mach3
devCad Cam Pro; devWing Cam; devFus Cam; Profili Pro 2
yes correct - you have it. Well done.
Steps... Speed... acceleration.
Z axis is slow on purpose to stop accidental cutter breaks 🙂
Remember the max feed rate (1800mm/min) is the max rate the machine can travel - giver her own weight, and drives etc. In reality - we machine down under 1000mm/min. depending on how well setup the machine is and what you are machining.

Hi @Rory
Could you please explain a bit
That is steps per unit - is such that the output from the machine (how far / fast is physically moves) is correct. For SC its 200 steps / unit (mm).
"
Stepcraft is direct drive (1:1 / motor turn:leadscrew turn)
It uses ST4118S1404-KUSO which is 200 steps per rotation.
However leadscrew is 3mm pitch. Thus 1 motor turn = 3mm linear movement, or if put otherwise, it takes 1/3 of full motor turn to lineary move machine 1mm.
Why are you suggesting Mach3 setting 200 steps/unit? Sure, it's 200 steps/full rotation, but it's not what this setting is about.
If you use this setting how are you milling details in correct sizes? 🙂 Say you hit "G0 Y-100.0" at Mach3 direct console, by your suggested settings it will move anything, but 100mm.
As I write I am setting up Mach3 -> Ethernet Smoothstepper -> Stepcraft 840 combo and I am at motor tuning process and also researching this forum on how others have set up their Mach3 - Stepcrafts.
Could you please comment on this?
Thanks.
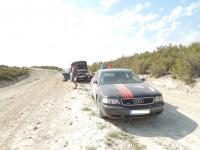
Steps per Unit:
400 Steps per 360°(half step) on older machines with 2mm per 360° = 200 Steps per mm.
400 Steps per 360°(half step) on newer -2 Modells with 3mm per 360° = 133.33 Steps per mm!!!
Motortuning start with 500mm/min, if everything is working like expected increase speed up to a Limit where you loose Steps or can't reach the Calibarationswitches.
And than use this Number -20%.
Regards,
Michael
there are 10 types of people in this world, those who understand binary and those who dont
Stepkraft 2 840++, Kress 1050, Mach 3, Estlcam, Corel Draw, VCarve, PhotoVCarve, Vakuumtisch, Absaugung.
Beruf: Informatiker und IT Security Experte
(++ = Bessere Steuerung, stärkere Stepper)

yes, these motors work in half microstepping and thus it is 133.33333(3) steps per unit (mm) and this is how is have set it up currently and it works 🙂
what dazzled me is why suggestion is to use 200.
what i did get from your answer and the thing that explains everything - "older machines with 2mm". i just assumed that the pitch has always been 3mm, my mistake! 🙂 all clear now.
as for speed currently i am going to the limits of the motors (the moment the motors stall due to pulse width), as i'm using smoothstepper and pc+msw stability for pusle generation is out of equation. currently at 2500 mm/min o_O for y axis and "kind of" not loosing steps (i even do not try to test this machine with higher travel speeds). need to g-code a "pen draw test" with many accelerated arcs and overrides to test these limits, especially how these motors handle torque in acceleration. using low weight hf spindle. thanks!
Same here. On the 840 200 steps per unit is way off. Hope somebody has the correct answer.

use the good ol mach3 calculator (zipped xls attached)
i already filled the fields for you to see how 2x microstepping creates the result
it is 1.33333333333 per unit (assuming you are using metric units)
Thank you! I tried that and the scale is way to small, basically reduced to just a point. Probably something else is wrong also but I can't figure it out yet. I just wish they would make a technical sheet with all those settings so we wouldn't have do experiment and loose so much time. Is that too much to ask?!
P.S. I use metric
I fiddled with it some more and 133.(3) is 100% correct. Thank you.
What throw me off was the fact that the sample file roadrunner is so small!
You would think that a sample file must be some sort of scale in mm and inches so you can accurately gauge what you are doing but instead we get a very small cartoon... LOL
Guys, the people at stoneycnc.co.uk helped me out. Although I didn't bought the 840 from them they offered to share with me the xml file for setting up the Stepcraft 840 with Mach3. My dealer had no freaking idea how to help me.
I am sure that if you have problems with your setup they will come to the rescue if you ask them nicely.
StoneyCNC... Thank you! 😉
good evening, I am a S2 840 new user, not a stoney cnc client, have no clue how to configure my 840 to 3d print on Mach3; I am using it via USB, I am pretty sure right now Mach3 does not even detect the machine. Manual jog does not work, the machine USB LED is off. Could you kindly share the xml file? I don't suppose that would solve it all in one shot, would it?
Best,
I sent you a PM!
thanks so much, last detail is a USB connection appropriate with this config?
- 44 Foren
- 7,333 Themen
- 63.2 K Beiträge
- 0 Online
- 26.3 K Mitglieder