Dear user, the forum software has been updated. For the first login please reset your password.
Stepcraft 420 it cuts a mm less in X
Good days, I have a Stepcraft 420, with LPT and UC100, use Cut2D and UCCNC, at first it seems to work likely but I have detected that in the axis X always cuts 1 mm. Less, that is to say if I do a rectangle of 50 x 50 give him 49 x 50 the cut measurements, if I do a rectangle of 100 x 100 mm it goes out for me 99 x 100 mm, I do not know correct like this mistake that is always 1 mm less in the axis X, the information of the file is equal in X and And. Someone might help. A greeting
🙁
hello - where did you get the profile for the UCCNC? can you send it to me? you can calibrate that out - but its unlikely its software.
STEPCRAFT drives are 200 steps per unit.
Make sure there is no mechanical backlash in the X axis - like play in the brass couplings etc..
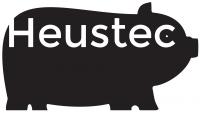
If you cut two lines from a central point in both X+ and X- are they both 1mm out?
It might be that the X axis is referencing too far away from the correct reference points? Just an idea.
When you calculate the toothpath with Cut2D are you going on the line, inside or outside the line? What thckness is the tool set to?
Alex
The drives have a pre defined setting for the motors.
The motors are the same
The calibration for the ballscrews are the same.
you need to check there is no mechanical movement in your system. It is most likely coming when you change direction in X.
this is a good test.
1) move the X in the positive direction
2) plunge into the work to 0.5mm
3) move in the X direction again (zero X and type in G01X20 into the MDI and she will move +20)
4) measure this - is it correct?
see what you find.
then type in G01X0 - and the machine should move back to 0. If there is backlash or mechanical movement in your system the machine will not come back to the same point.
you can calibrate the axis by asking "please move the axis 50mm"... then it moves... and the you can tell it how far it has moved. But the problem is almost for sure - the mechanical performance
- 44 Foren
- 7,336 Themen
- 63.2 K Beiträge
- 1 Online
- 26.3 K Mitglieder